Markforged Resources
Customer Success Stories
Learn
Blog
Customer Success Stories
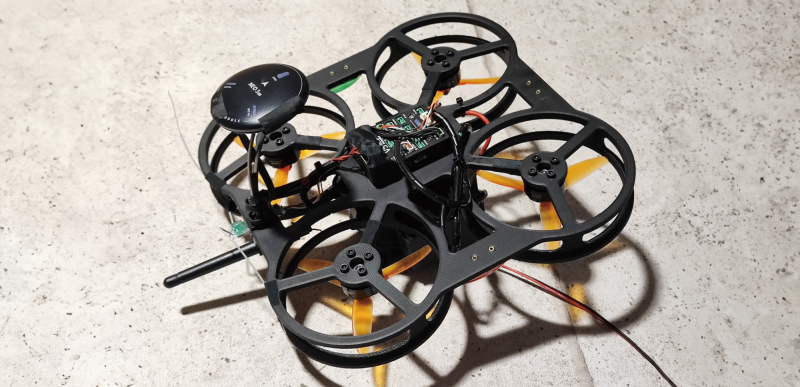
BODUK Co., Ltd.
Explore how BODUK Co., Ltd. has enhanced its industrial drone manufacturing operations. Utilizing Markforged, BODUK has achieved a significant reduction in production times.
Learn
Blog
Customer Success Stories
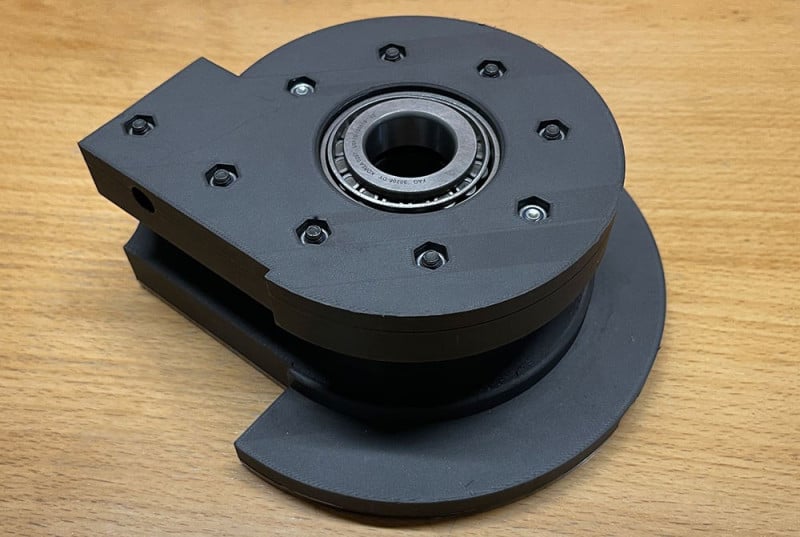
Toivalan Metalli
Toivalan Metalli, a Finnish metalwork company, leverages the Markforged X7 printer to create tube-bending tools and end-use parts, substantially reducing production costs and lead times for custom and low-volume projects.
Learn
Blog
Customer Success Stories
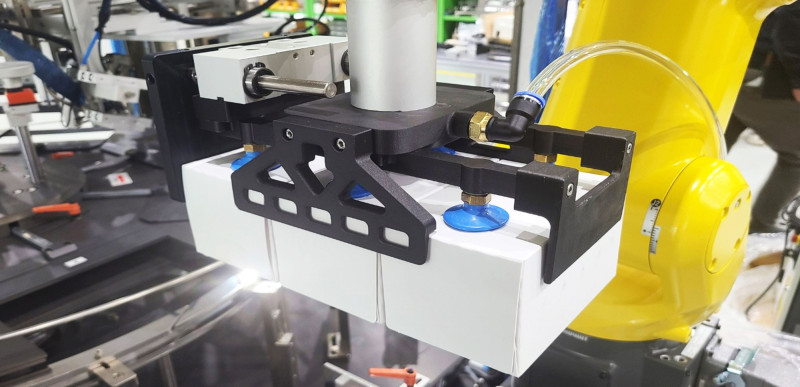
Harvestance
Harvestance improves production line robotics by leveraging Markforged's technology to create customized, lightweight, and strong vacuum grippers for collaborative robots. These advanced grippers reduce weight by 80% compared to conventional models, significantly enhancing robot performance and energy efficiency, while slashing delivery times from weeks to just days.
Learn
Blog
Customer Success Stories
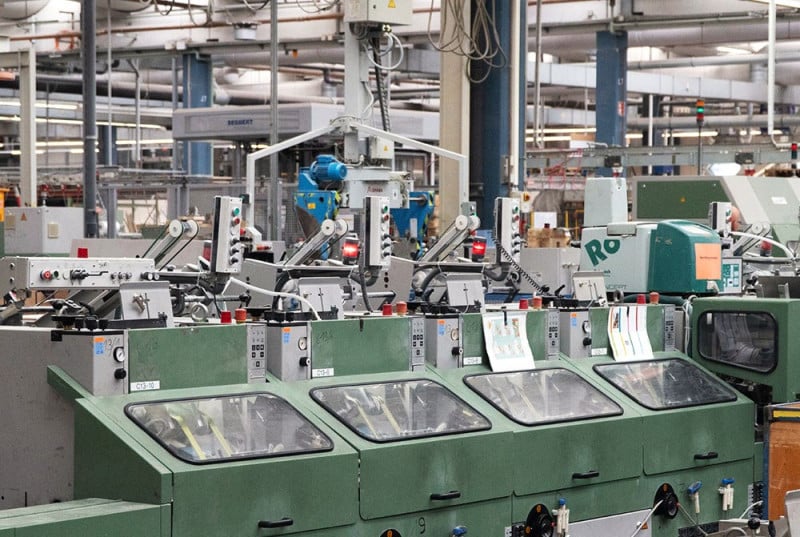
Vogel Druck
Vogel Druck enhanced its printing services by incorporating Markforged's Mark Two 3D printers, enabling the swift production of spare parts and reducing operational costs. This strategic move demonstrates the company's proactive approach to leveraging additive manufacturing for greater efficiency and cost savings.
Learn
Blog
Customer Success Stories

AMPC
Discover how the Australian Meat Processor Corporation (AMPC) transforms the meat processing industry by leveraging Markforged's additive manufacturing technology. This innovative collaboration ensures continuous equipment operation, minimizing downtime and significantly cutting costs through the on-demand production of critical parts.
Learn
Blog
Customer Success Stories
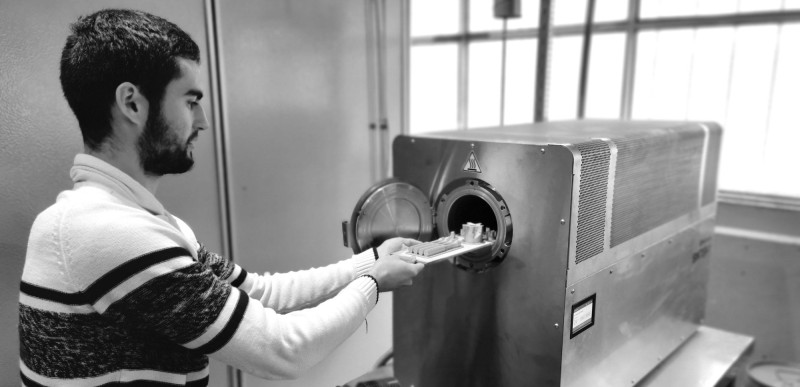
Goierri Eskola
Goierri Eskola, an educational institution in Spain's Basque Country, has significantly advanced its training capabilities and industry collaboration by integrating the Markforged Metal X system into its curriculum.
Learn
Blog
Customer Success Stories
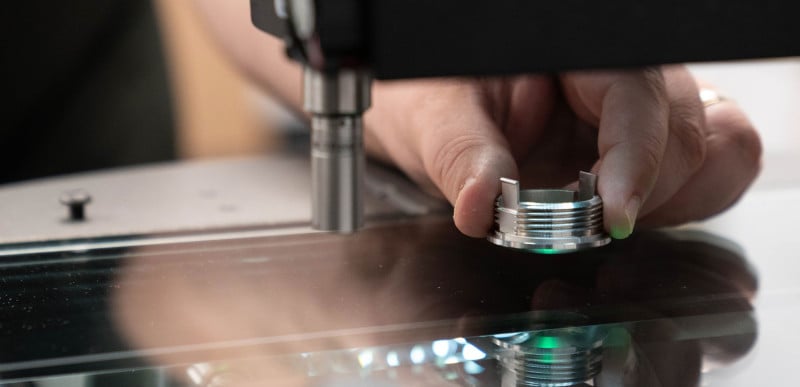
PTI Tech
PTI Tech uses Markforged metal binder jetting to accelerate MIM prototyping, significantly reducing the development time and cost for high-precision, durable elevator button assemblies. This innovative approach bypasses traditional pre-production tooling, allowing for rapid prototyping and efficient design validation.
Learn
Blog
Customer Success Stories
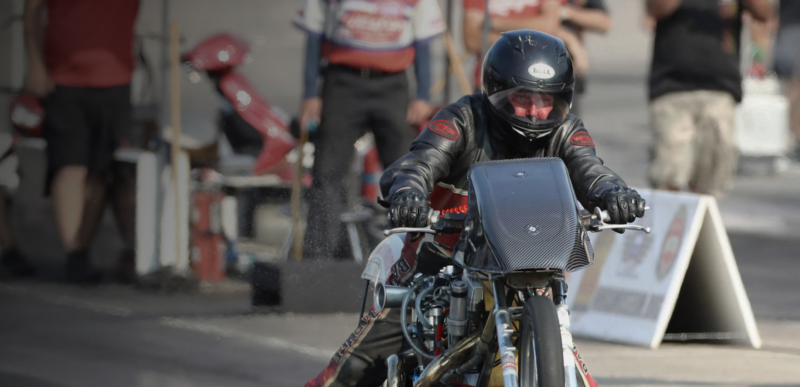
Hawaya Racing, Inc
Hawaya Racing specializes in the research, development, and manufacturing of Harley-Davidson drag racing motorcycle parts and safety equipment. In 2022, Hawaya Racing, Inc. purchased a Markforged X7 through Phillips Corporation. The X7 was chosen for its ability to replace CNC-machined parts with highly durable composites using Continuous Fiber Reinforcement (CFR).
Learn
Blog
Customer Success Stories
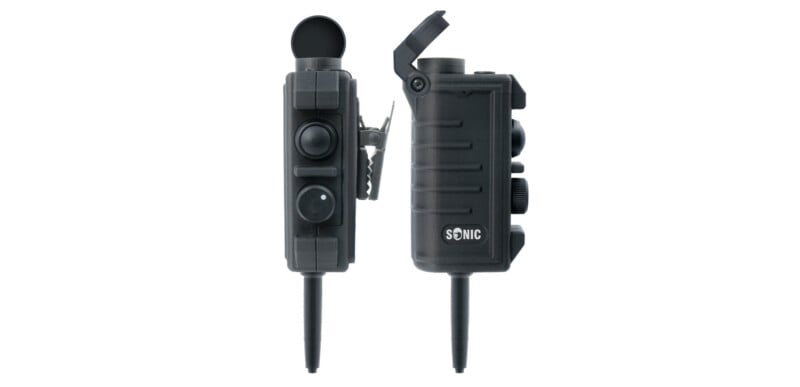
Sonic Communications
With Markforged, Sonic Communications can go from design to final product in a quarter of the time it would take with in-house machining.
Learn
Blog
Customer Success Stories
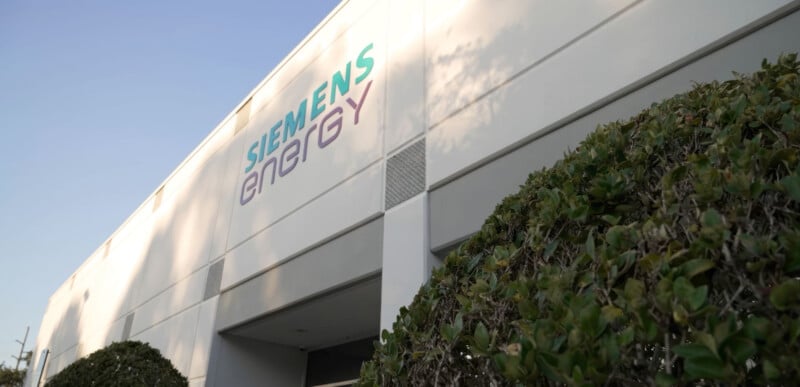
Siemens Energy Technology Application Center
Siemens Energy uses Simulation for fast and accurate structural analysis of part designs— allowing fast print times for structurally sound parts.