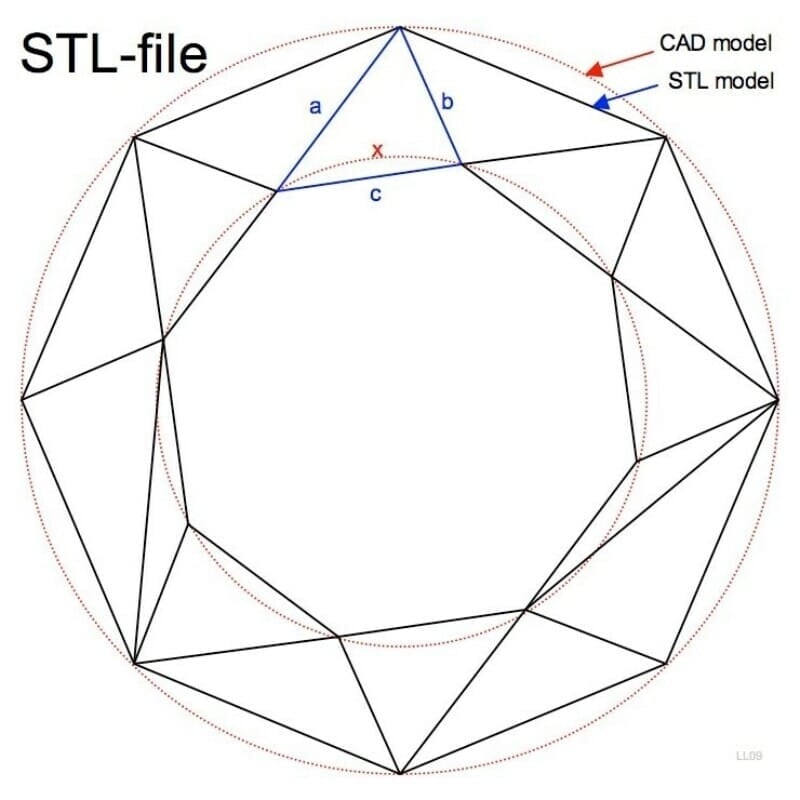
An Intro to STL Files
As 3D printing becomes increasingly accessible, so will the technology that makes it all possible. Already, companies from a myriad of backgrounds are tracking 3D printing organizations like Pinshape and YouMagine, to get a glimpse of how this amazing technology works. As should you, because once it becomes more accessible, you will want to know a few things about it. Like STL files, known as “Standard Triangle Language” or “Stereolithography”, the most necessary component of all.
STL files take an image from a CAD model, which is used to visually create a virtual design; STL files also provide a reference point from which that object is printed.
Two Types of STL Files
There are two types of these files: ASCII and binary. While binary files are much smaller and used more often, ASCII files are easier to tweak and modify over time. In terms of functionality, these files are often used to the same effect.
Think virtual cookie cutter. These files essentially define an objects parameter and overall shape by using coordinates to transfer the data required to print the dimensions of each object.
It’s possible that STL files are as important as the CAD model itself, since they act as the primary medium, transferring designs from a virtual concept to a physical object.
STL Files are Easily Found Online
They are also readily accessible online. In fact, people are now sharing STL files on the web, and these files can be downloaded right to your computer. If you’re interested in finding this out for yourself, Thingiverse is a resourceful place to start.
It’s Made of Triangles, Lots of Primitive Triangles
The significance behind STL files is geometry, namely the Cartesian coordinate system. Using three-dimensional triangles, STL files act as virtual grids, each containing a collection of facets that act as a boundary between the interior and the exterior of each object. These facets are used much like a ruler to satisfy the vertex-to vertex rule: all facets must share two sides with its adjacent triangle to create a positive octant; and all coordinates must be positive to meet this requirement.
Think about it? To be transformed into a solid object, STL files must have connecting sides with corresponding units. If this weren’t the case, there would be no way to form those objects. It would be as if you were trying to connect two parts of a bridge with different sized beams.
All of the blogs and the information contained within those blogs are copyright by Markforged, Inc. and may not be copied, modified, or adopted in any way without our written permission. Our blogs may contain our service marks or trademarks, as well as of those our affiliates. Your use of our blogs does not constitute any right or license for you to use our service marks or trademarks without our prior permission. Markforged Information provided in our blogs should not be considered professional advice. We are under no obligation to update or revise blogs based on new information, subsequent events, or otherwise.
Never miss an article
Subscribe to get new Markforged content in your inbox