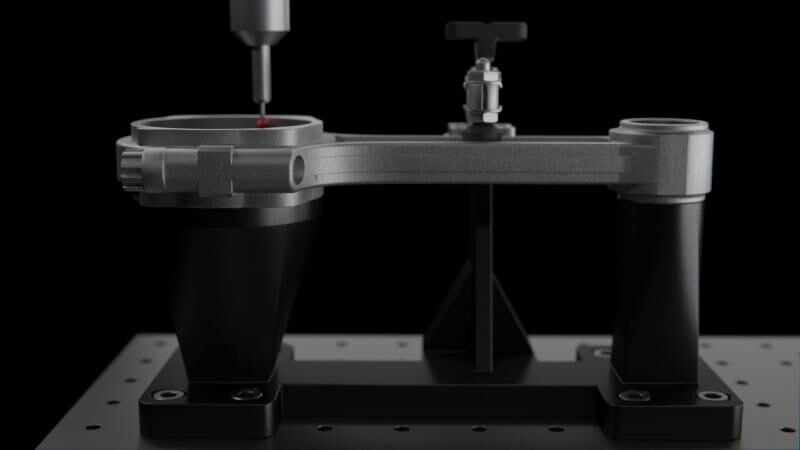
Inspection Fixtures — Traditional Machining vs Additive Manufacturing
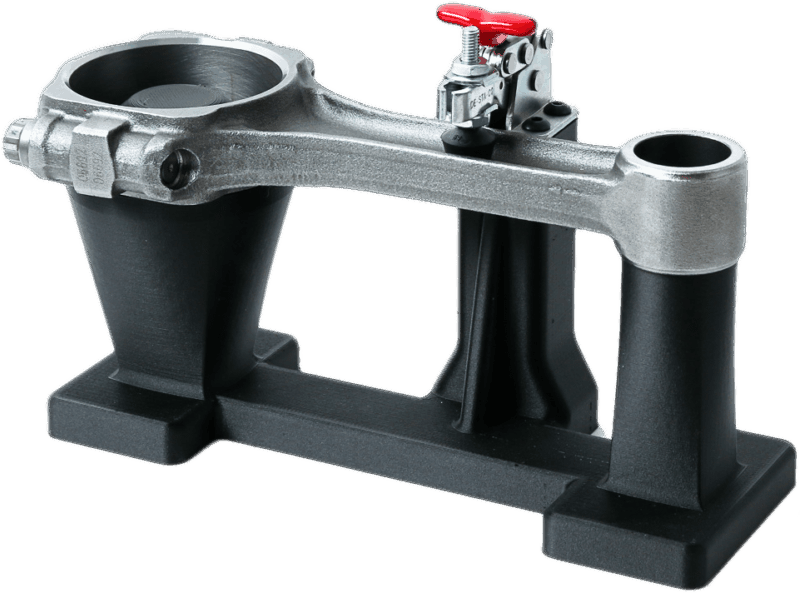
Traditionally manufacturing inspection fixtures
Inspection is a routine component of the manufacturing process; as parts come off of the production line, some are examined to ensure accurate dimensions. This process requires specialized workholding. Two examples include CMM fixtures and check gauges.
A coordinate-measuring machine (CMM) is a precision tool that probes multiple points on a part to determine if the geometry is within specification. Check gauges are another form of inspection fixture used to quickly and accurately determine if parts are satisfying basic tolerances. If the part fits into the gauge, the part is within specification.
These fixtures need to satisfy stiffness and precision requirements, which traditionally would mean they would be custom-machined out of aluminum. However, the process is expensive and depletes valuable shop time. As the effort increases with the complexity of machined parts, it becomes even more cumbersome to manufacture inspection fixtures that must contain intricate geometries.
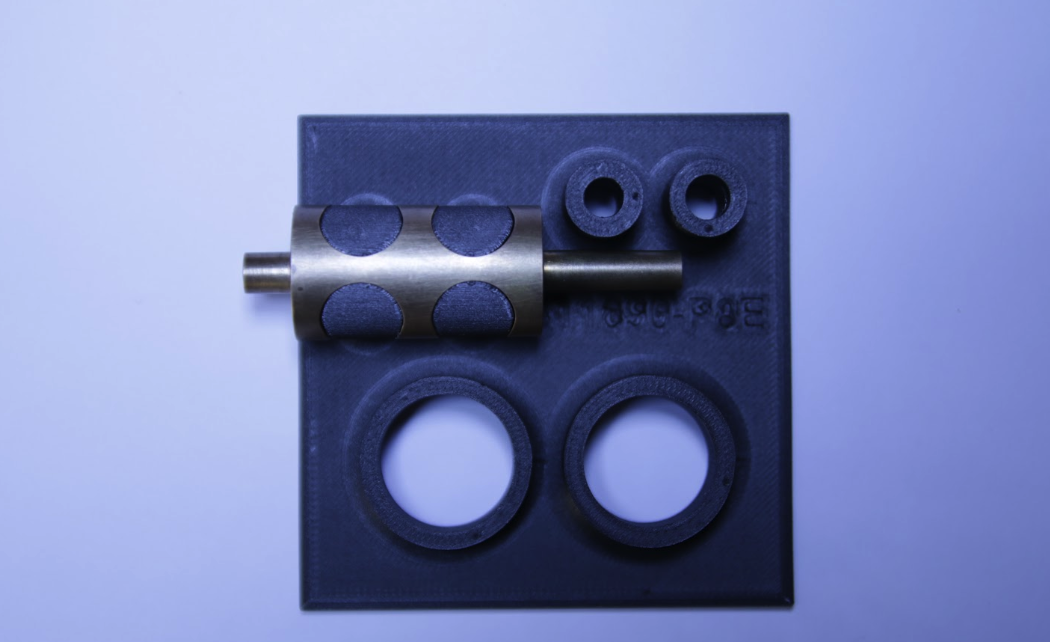
Why machining complex parts is hard
With 3-axis mills, complexity is already restricted by machine-specific limitations, such as the inability to perform undercuts. This renders certain geometries unproducible and forces you to constrain the complexity of your design to those restrictions.
After your part is designed for traditional manufacturing, it’s not ready to be fabricated quite yet. If a fixture is to be machined, it must be prepared in CAM beforehand. This process involves selecting which tools will be used to cut the stock and planning out the paths for each of those tools. Because more complex geometries often require a higher number of cutting operations, more intricate parts make for more work in CAM, and more skilled labor spent on fabricating the part. Alternatively, utilizing composite 3D printing to manufacture fixtures allows you to produce stiff, precise workholding while cutting out the expensive, time-consuming CAM process. Eiger, Markforged’s slicing software, takes care of all of the preparation; so all you have to do is design, then start the print. Higher geometric complexity can be printed with no extra effort, allowing for intricate, form-fitting fixtures to be produced at a lower cost.
To learn more about how composite 3D printed inspection fixtures help save time and money, watch the webinar. Or check out our case study on how JJ Churchill used Markforged printers to produce CMM fixturing 70% faster for 80% less cost.
Request a free sample part to test the strength of our materials!
All of the blogs and the information contained within those blogs are copyright by Markforged, Inc. and may not be copied, modified, or adopted in any way without our written permission. Our blogs may contain our service marks or trademarks, as well as of those our affiliates. Your use of our blogs does not constitute any right or license for you to use our service marks or trademarks without our prior permission. Markforged Information provided in our blogs should not be considered professional advice. We are under no obligation to update or revise blogs based on new information, subsequent events, or otherwise.
Never miss an article
Subscribe to get new Markforged content in your inbox