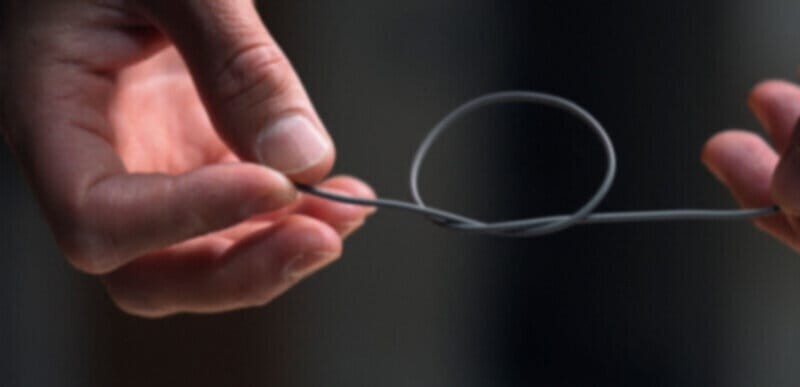
17-4PH Stainless Steel v2: Same Metal, New Binder
17-4PH is a general purpose stainless steel alloy, frequently utilized for its strength and ability to withstand significant wear, heat, and corrosion. It can be heat treated, polished, machined, welded, and 3D printed. It is often used for industrial applications such as grippers, lathe jaws, fixtures, brackets, high-wear tooling, functional prototypes, and custom wrenches and sockets.
17-4PH filament is the Metal X System’s most popular metal material. Updating the Metal X System’s first 17-4PH formulation with a new binder material makes this stainless steel filament easier for users to handle and print parts.
Read about the benefits of using our updated 17-4PH v2 filament, which features an updated binder material — along with a review of metal FFF (fused filament fabrication) filaments and how the metal FFF 3D printing process works.
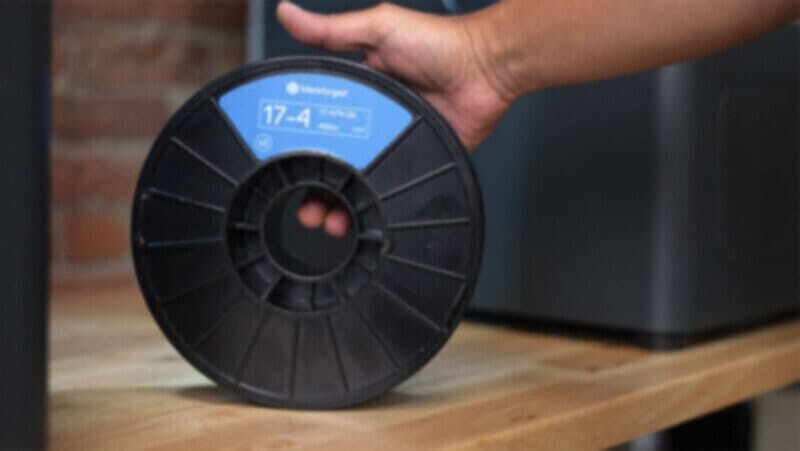
Comparing 17-4PH Stainless Steel Filaments: v1 and v2
The 17-4PH Stainless Steel v2 filament for the Metal X features the same metal powder with an updated binder material.
Preserving the v1 filament’s strength, durability, and corrosion resistance, v2’s updated binder material results in a significantly more flexible and less brittle filament. The metal powder is exactly the same. Altering the composition of the binder — with a new material and percent volume — is what produces 17-4PH v2 filament’s improved material properties.
Compared to v1, 17-4PH v2 on the Metal X is easier to handle. It’s more flexible, making it easy to store, easy to handle at room temperature, and far less fragile. 17-4PH v2 also features improved mechanical properties, being stronger and with better isotropic characteristics.
The v2 formulation is also faster to load and comes in larger spools. It can be loaded into an unheated chamber, and print for twice as long before the spool of filament must be replaced. This significantly reduces startup and material changeover times.
Printing 17-4PH Stainless Steel
The Metal FFF Process
Fused filament fabrication (or FFF) 3D printers work by extruding a spool filament through a hot nozzle to additively build a part layer by layer. Filaments come in different sizes and materials ranging from prototype plastics, industrial thermoplastics, and metals. Metal FFF is capable of printing in a wide variety of metals: such as tool steels, stainless steels, pure copper, and superalloys such as Inconel.
Metal FFF works by incorporating processes from metal injection molding (MIM) into the FFF printing process. It uses MIM feedstock, but instead of injecting it into a mold, it uses the FFF 3D printing process to form the part layer by layer. After the fabrication process, metal FFF uses the same subsequent two steps as MIM: debinding and sintering.
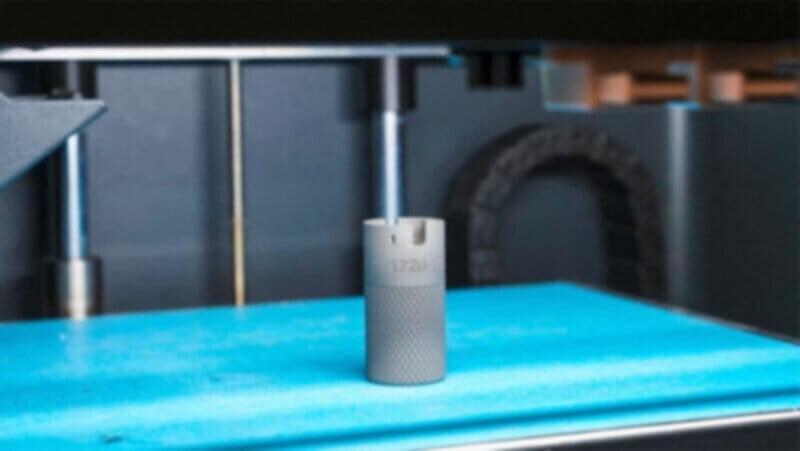
Metal FFF Filaments
Metal FFF filaments have a unique combination of metal powder, polymer, and wax. The polymer and wax act together as a binder that keeps the metal powder bound together during the printing process.
Encapsulating metal powder in these binders is a massive advantage from a safety and usability standpoint: it makes metal FFF printing very safe and easy to use compared to other metal 3D printing technologies. Users can effectively handle the filament without the need for respirators, Hazmat suits, and explosion proof equipment.
When the print head extrudes the filament, the nozzle is set to the melting point temperature of the binder and the metal powder goes along for a ride. The next two steps of the process — debinding and sintering — are critical to remove the other ingredients and ultimately arrive at a fully formed metal part.
Download the Metal FFF 3D Printing Applications Guide
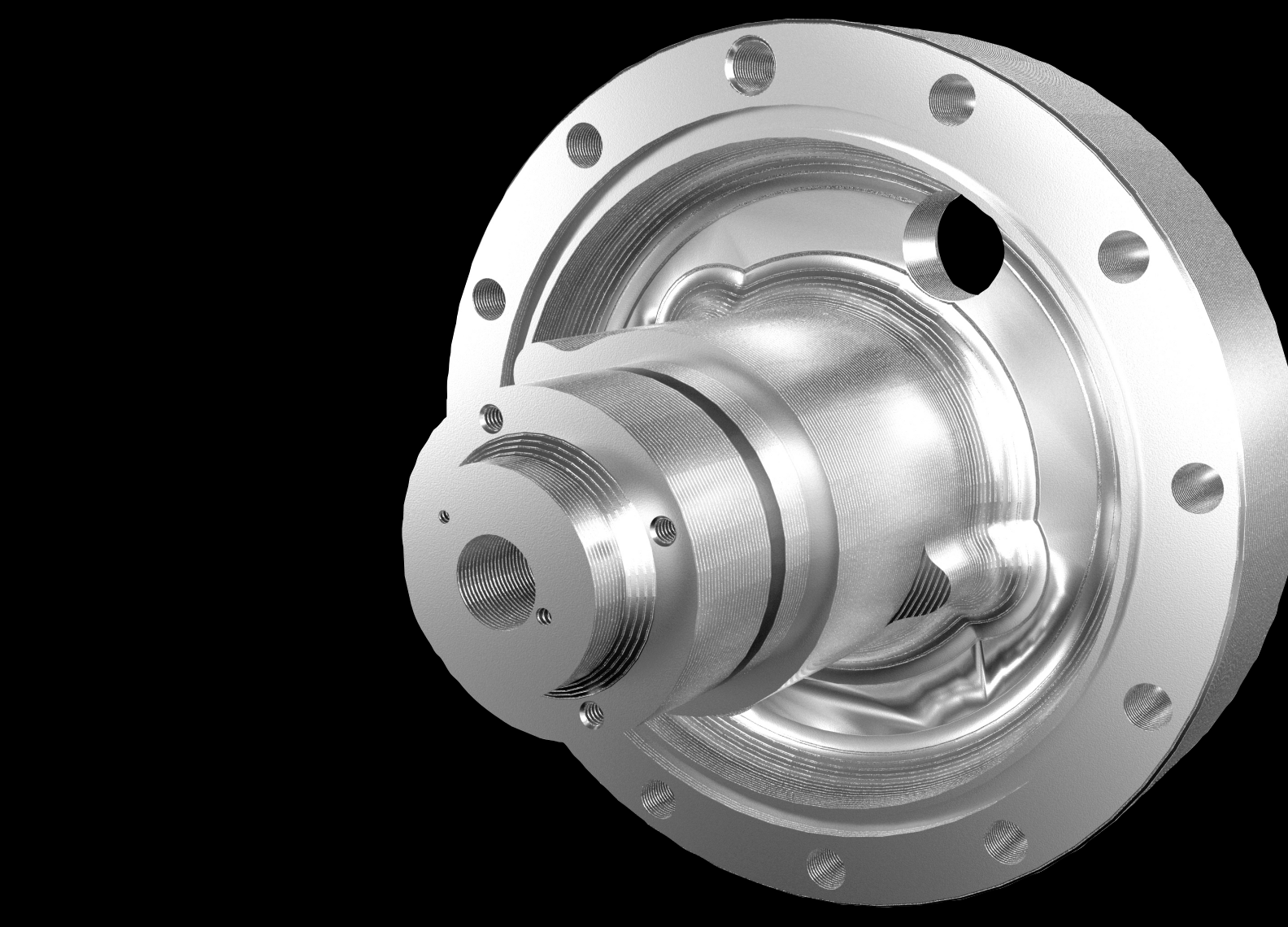
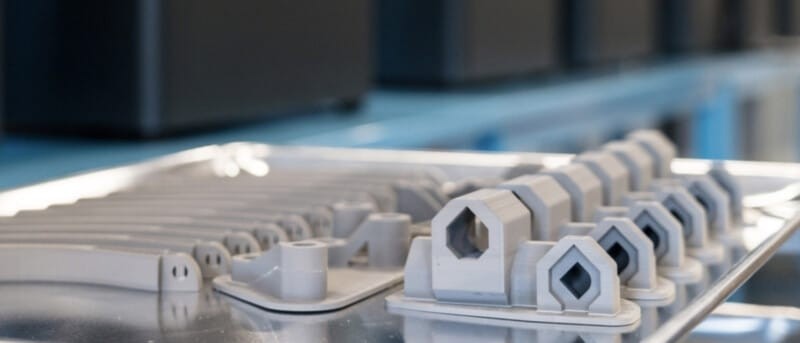
How the Metal FFF 3D Printing Process Works
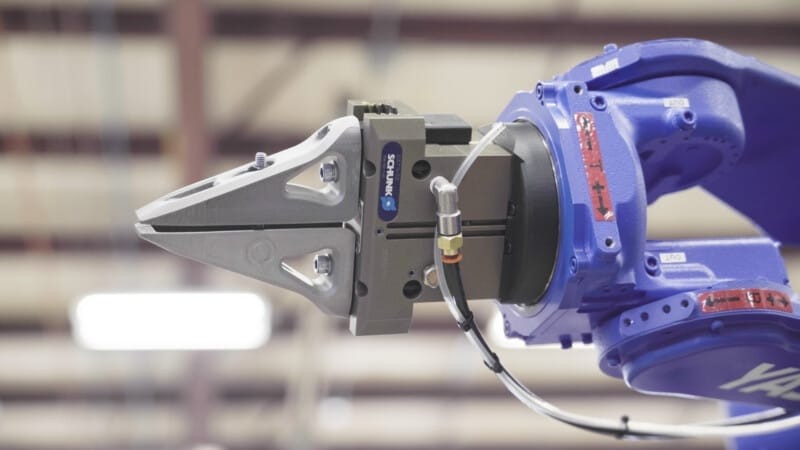
Inconel vs Stainless Steel
All of the blogs and the information contained within those blogs are copyright by Markforged, Inc. and may not be copied, modified, or adopted in any way without our written permission. Our blogs may contain our service marks or trademarks, as well as of those our affiliates. Your use of our blogs does not constitute any right or license for you to use our service marks or trademarks without our prior permission. Markforged Information provided in our blogs should not be considered professional advice. We are under no obligation to update or revise blogs based on new information, subsequent events, or otherwise.
Never miss an article
Subscribe to get new Markforged content in your inbox