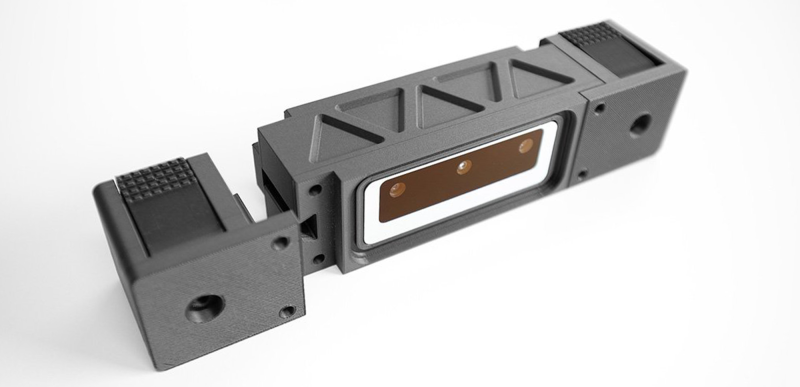
CADDS Group - KI-Gehäuse
Die CADDS-Gruppe mit Sitz in Westaustralien beschäftigt mehr als 180 Mitarbeiter in ihren sechs Abteilungen Vermessung, Technisches Design, Produktdesign, Gebäudeplanung, Nachhaltiges Umweltdesign und Fertigung. Jede Abteilung deckt ein breites Spektrum an Dienstleistungen für die größten Unternehmen des Bundesstaates ab. Zu den Blue Chip-Kunden aus dem Bergbausektor gehören namhafte Unternehmen wie Rio Tinto, BHP, Alcoa und die Forschungseinrichtung der Australischen Regierung CSIRO.
2023 hat die CADDS Group ihre Fähigkeiten durch eine Investition in drei hochmoderne Markforged-Drucker (FX20™, Mark Two™ und Metal X™ ) strategisch erweitert. Mit diesen hochmodernen Geräten ist die Gruppe in der Lage, Teile und Werkzeuge mit hoher Festigkeit und unvergleichlicher Präzision zu fertigen, so Geschäftsführer Darren Clark. Durch die Verwendung neuester Materialien wie Endloscarbonfaser, Edelstahl, Kupfer und Werkzeugstahl katapultiert die Technologie das Unternehmen an die Spitze der Innovation.
Norbert Babooram, Product Design Manager von Inovaus, der Produktdesign-Abteilung der CADDS-Gruppe, sagte, dass sich der Zugang zu eigenen Druckanlagen im Unternehmen als zeitsparendes Werkzeug für Brainstorming erwiesen hat. „Bevor wir die Drucker hatten, mussten wir mögliche Lösungen für ein Problem durchgehen und entscheiden, welche von mehreren Ideen wir verfolgen wollten. Heute können wir ganz einfach mehrere Ideen ausprobieren. Es ist eine großartige Möglichkeit, Bauteile zu testen und Designrichtungen zu bestätigen“, sagte er.
Diese Flexibilität wurde kürzlich genutzt, als Inovaus mit der Entwicklung eines Gehäuses für eine Kamera beauftragt wurde, die einen kleinen aber wichtigen Teil eines KIgesteuerten mobilen modularen Werkstattsystems für ein großes Bergbauunternehmen bildet. Das Gehäuse musste die Kamera vor den rauen, staubigen Bedingungen am Produktionsstandort der Mine schützen. Da das System außerdem an verschiedenen Standorten eingesetzt werden sollte, musste es eine Reihe flexibler Systeme für jeden Standort besitzen.
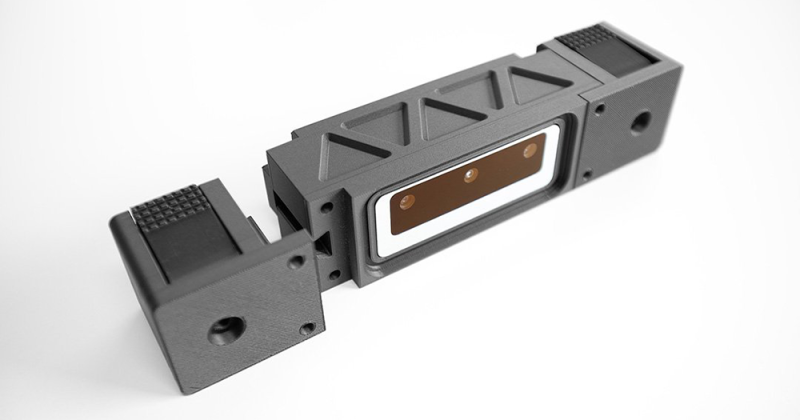
Nachforschungen hatten ergeben, dass es keine Lösung von der Stange gab und dass ein maßgeschneidertes Gehäuse von Grund auf neu entwickelt werden musste. Laut Babooram war es sehr hilfreich, selbst einen Drucker im Unternehmen zu haben. Mit diesem wurde der erste Prototyp innerhalb von drei Tagen hergestellt. Das Team entwickelte zwei Befestigungslösungen, eine zum Klemmen und eine magnetische, um eine flexible Montage zu ermöglichen. „Das Schöne an der Qualität und Stärke des Druckvorgangs ist, dass aus dem Prototyp durch einige geringfügige Änderungen nun das fertige Produkt entstanden ist, das sofort einsatzbereit ist“, so Babooram.
„Vor der Anschaffung der Anlagen für die Additive Fertigung hätten wir für die Fertigung Kunststoffe im Spritzgussverfahren verwenden müssen. Wir wären nicht flexibel gewesen, um Prototypen zu testen. Hätte einer nicht funktioniert, wäre die Herstellung neuer Prototypen zeitaufwändig gewesen. Alles in allem hätte die Entwicklung wahrscheinlich etwa zwei Monate gedauert, um die richtige Form zu finden. Concept bestätigte das Bauteil in weniger als zwei Wochen und hatte innerhalb dieser Zeit ein gebrauchsfertiges Produkt, das nicht mithilfe einer maschinellen Bearbeitung oder Spritzgießen hergestellt wurde.
„Auch die wirtschaftlichen Aspekte sind beeindruckend. Wir haben eine Kalkulation für das Spritzgussverfahren angestellt, die Kosten von 55.000 $ einschließlich Entwicklungskosten vorhersah, wobei die Mindestmenge weit über unserem Bedarf lag. Die Herstellung der Gehäuse auf unserem Drucker ist bereits ab einem Preis von 800 $ pro Stück möglich. Außerdem ist die Produktion in kleinen Stückzahlen möglich, wodurch die Zeit- und Kosteneinsparungen enorm sind“, sagte er.
Die industrietauglichen 3D-Drucker von Markforged bieten der Bergbauindustrie durch das einzigartige Digital Forge-Ökosystem des Unternehmens wichtige Vorteile, die den Betrieb, die Leitung und die Überwachung von Minenstandorten aus der Ferne ermöglichen. Diese Technologie wird es der CADDS-Gruppe ermöglichen, hochleistungsfähige Teile und Komponenten vor Ort zu produzieren, was die Vorlaufzeiten verkürzt, Stillstandszeiten minimiert und die betriebliche Effizienz insgesamt verbessert.
— Norbert Babooram Product Design Manager, Inovaus“Die Zeit- und Kosteneinsparungen sind enorm."
All of the blogs and the information contained within those blogs are copyright by Markforged, Inc. and may not be copied, modified, or adopted in any way without our written permission. Our blogs may contain our service marks or trademarks, as well as of those our affiliates. Your use of our blogs does not constitute any right or license for you to use our service marks or trademarks without our prior permission. Markforged Information provided in our blogs should not be considered professional advice. We are under no obligation to update or revise blogs based on new information, subsequent events, or otherwise.
Never miss an article
Subscribe to get new Markforged content in your inbox