Markforged Resources
Learn
Learn
Blog
Customer Success Stories
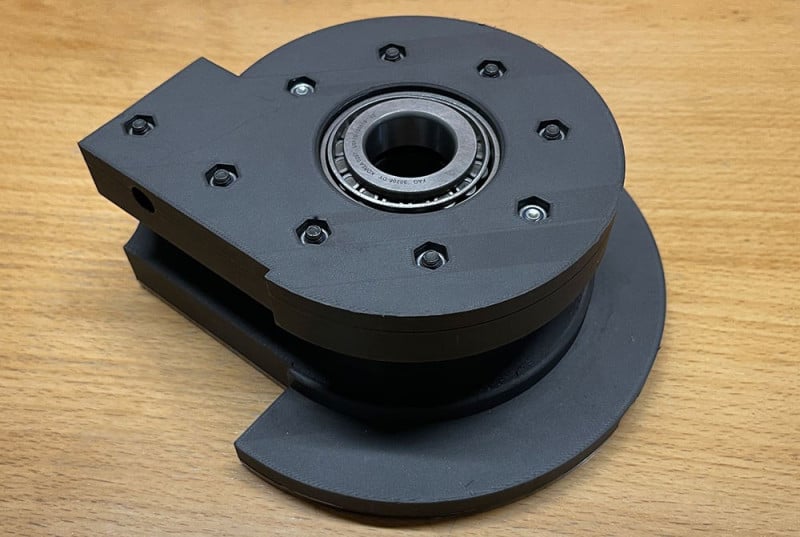
Toivalan Metalli
Toivalan Metalli es una empresa finlandesa de metalurgia que utiliza la impresora X7 de Markforged para crear herramientas de curvado de tubos y piezas de uso final, lo que le permite reducir sustancialmente los costes de producción y los plazos de entrega de proyectos personalizados y de bajo volumen.
Learn
Blog
Customer Success Stories
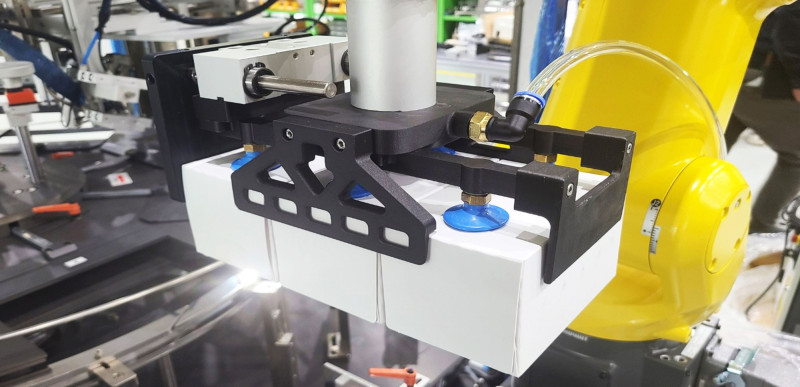
Harvestance
Harvestance mejora la robótica de las líneas de producción utilizando la tecnología de Markforged para crear pinzas de vacío personalizadas, ligeras y resistentes para robots colaborativos. Estas modernas pinzas reducen el peso en un 80 % en comparación con los modelos convencionales, mejorando significativamente el rendimiento del robot y la eficiencia energética, además de reducir los plazos de entrega de semanas a unos pocos días.
Learn
Blog
Application Spotlights
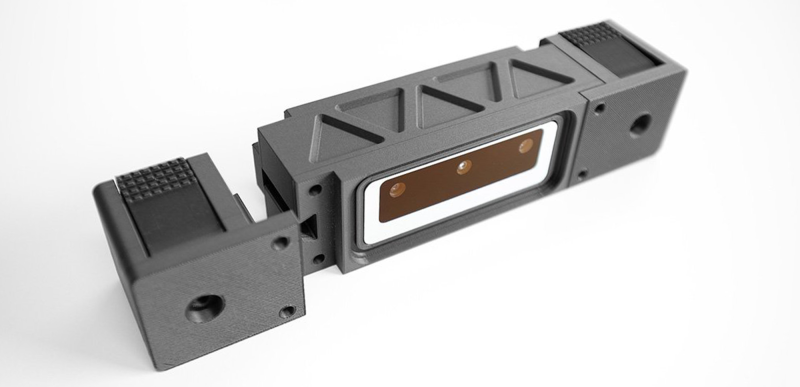
CADDS Group - Carcasa con IA
CADDS Group mejoró sus capacidades de ingeniería y diseño incorporando la tecnología de impresión 3D de Markforged, agilizando la producción de una carcasa de cámara de IA personalizada para el sector minero.
Learn
Blog
Application Spotlights
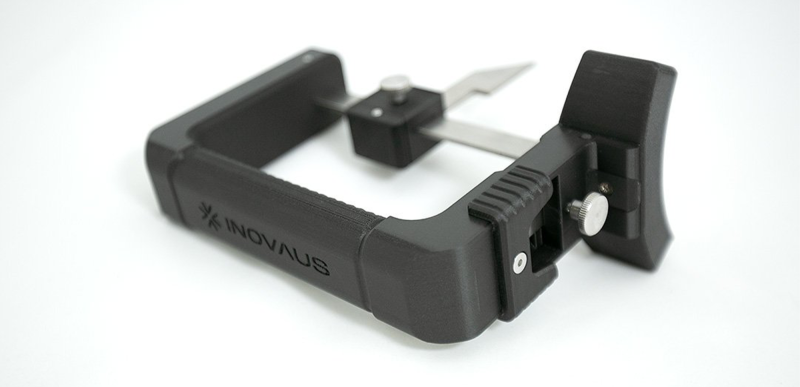
CADDS Group - Calibrador de mecanismos de tracción
CADDS Group aprovechó la tecnología de impresión 3D de Markforged para crear un calibrador de mecanismos de tracción más eficaz y rentable, mejorando su oferta de servicios a los principales clientes del sector minero.
Learn
Blog
Customer Success Stories
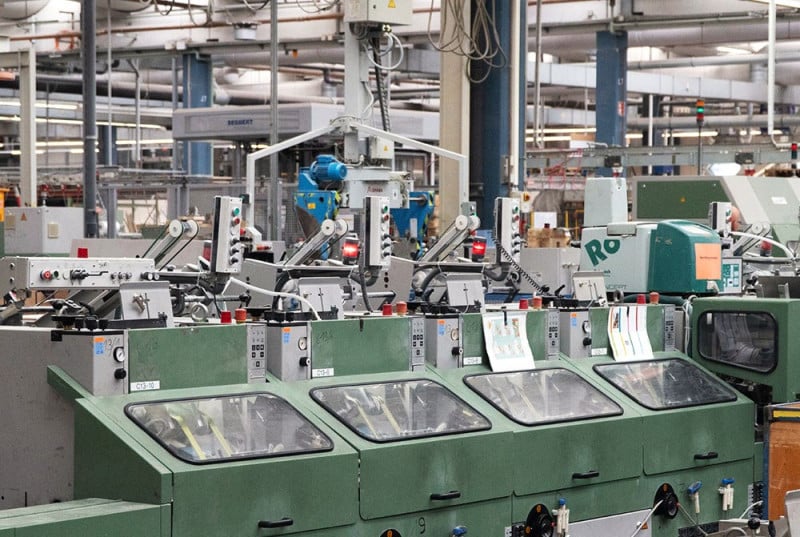
Vogel Druck
Vogel Druck mejoró sus servicios de impresión incorporando las impresoras 3D Mark Two de Markforged para producir piezas de recambio con rapidez y reducir los costes operativos. Este movimiento estratégico demuestra el enfoque proactivo de la empresa a la hora de utilizar la fabricación aditiva para lograr una mayor eficiencia y ahorro de costes.
Learn
Blog
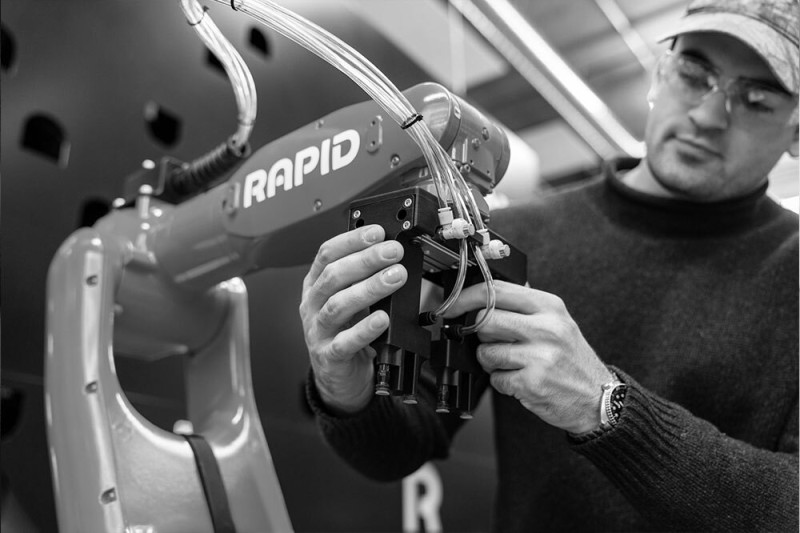
El papel clave de la impresión 3D en la producción de alimentos y bebidas
Los líderes del sector de alimentos y bebidas mantienen las líneas en funcionamiento con piezas de mantenimiento, reparación y revisión y herramientas de producción bajo demanda. Mejorar el rendimiento, optimizar los cambios de línea y garantizar la seguridad de los operarios son aspectos cruciales con la creciente adopción de la automatización en las fábricas.
Learn
Blog
Application Spotlights
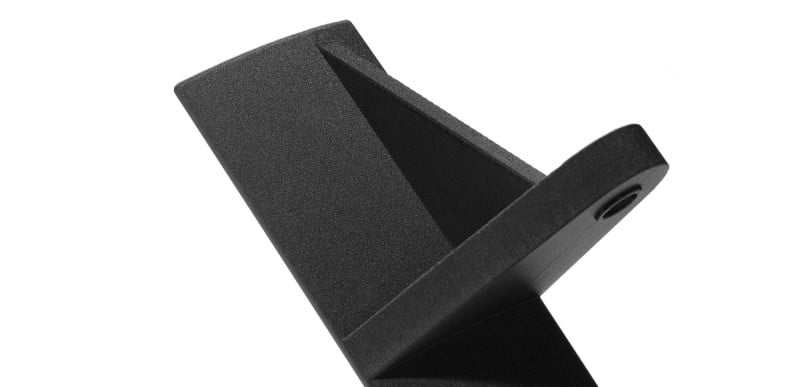
Protecciones personalizadas
Descubra cómo las innovadoras tecnologías de fabricación aditiva de Markforged están mejorando la seguridad en las industrias de alimentos y bebidas y de envasado. Al producir las protecciones personalizadas directamente en la fábrica, los equipos de producción pueden abordar los problemas de seguridad con rapidez, garantizando que las operaciones se ajusten a los protocolos de seguridad de forma eficaz y sin retrasos.
Learn
Blog
Application Spotlights
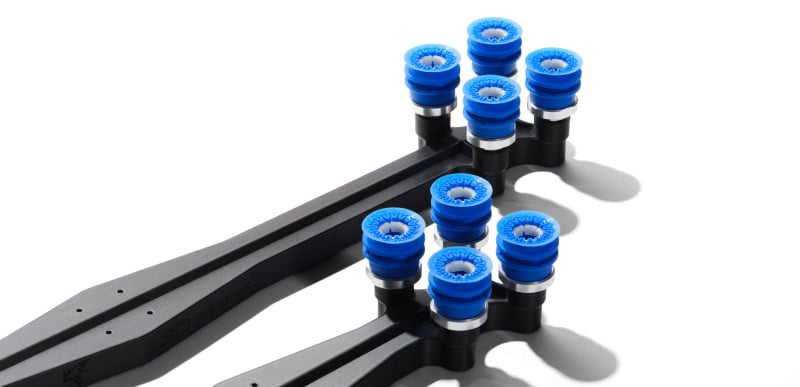
Herramientas de fin de brazo de producción
Descubra cómo Markforged transforma las industrias de alimentos y bebidas y de envasado utilizando la fabricación aditiva para crear herramientas de fin de brazo de producción. Esta aplicación destacada muestra la agilidad y eficiencia logradas en la fabricación mediante soluciones personalizables bajo demanda que utilizan la tecnología de fabricación aditiva de Markforged, mejorando significativamente la flexibilidad operativa y reduciendo los costes.
Learn
Blog
Application Spotlights
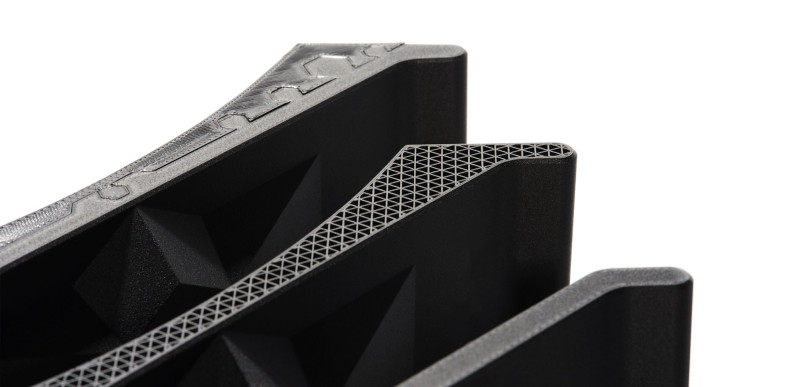
Placa de empuje personalizada
Descubra cómo la tecnología de fabricación aditiva de Markforged mejora las líneas de producción de los sectores de alimentos y bebidas y de envasado al permitir soluciones personalizables bajo demanda que mejoran la automatización y la eficacia, especialmente mediante el desarrollo de componentes personalizados como las placas de empuje.
Learn
Blog
Customer Success Stories

AMPC
Descubra cómo Australian Meat Processor Corporation (AMPC) moderniza el sector de la transformación cárnica mediante la tecnología de fabricación aditiva de Markforged. Esta innovadora colaboración garantiza el funcionamiento continuo de los equipos, minimizando el tiempo de inactividad y reduciendo considerablemente los costes gracias a la producción bajo demanda de piezas críticas.