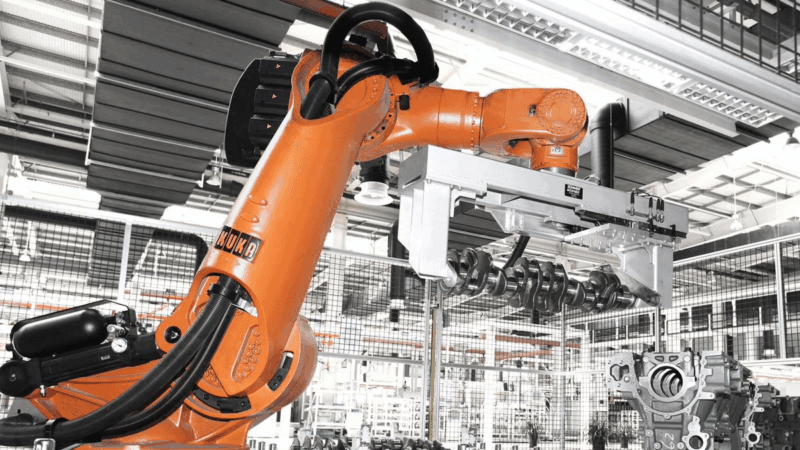
Industry 4.0 in the Context of Professional 3D Printers
Professional 3D printers today use augmentative technologies — such as cloud connectivity, data analytics, automation, and software integrations — to help manufacturers leverage each printer in new and innovative ways.
The addition of these technologies into professional 3D printers is part of the digital transformation of manufacturing, commonly known as Industry 4.0. Read this blog to learn what Industry 4.0 is in simple terms, the role of today’s professional 3D printers in Industry 4.0, and examples of how additive manufacturing platforms use Industry 4.0 technologies to provide solutions for problems.
Defining Industry 4.0
McKinsey & Company defines Industry 4.0 as a name for the broader “digitization of the manufacturing sector” — what this translates to more specifically is the application of emerging technologies into manufacturing facilities to improve processes.
Key themes and characteristics of Industry 4.0 include:
- The ability for different devices and machines within the factory — such as printers and sensors — to digitally send and receive information from each other.
- Collection of data from sensors in machines and devices within the factory for monitoring.
- The ability for technological systems to 1.) augment human decision-making, and 2.) facilitate completion of unsafe physical tasks.
- A shift towards smart, automated systems that require minimal human oversight.
Specific technologies that have fueled Industry 4.0 include cloud computing, artificial intelligence (AI), the industrial Internet of Things (IoT), data analytics, industrial robotics systems, professional 3D printers, and big data. While these individual technologies were not developed for the express purpose of use in smart factories, Industry 4.0 describes the growth and maturation of their application to factory settings.
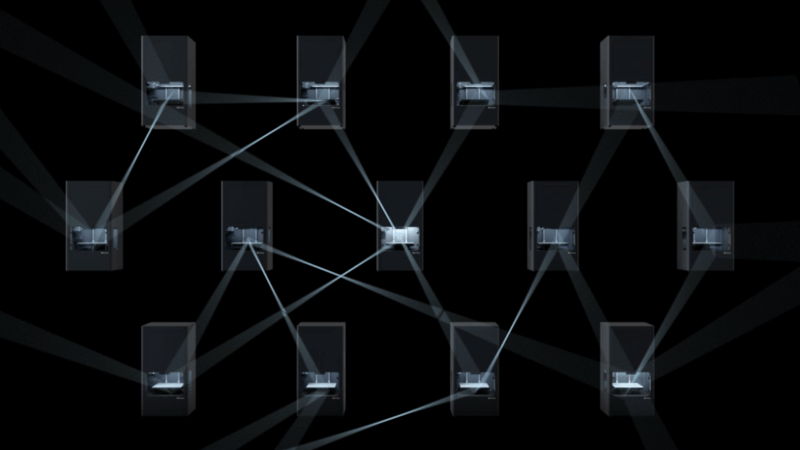
The Relationship Between Industry 4.0 and Additive
Additive manufacturing is a technology native to Industry 4.0. Converting digital inputs to physical outputs, digital inventory in the form of CAD files is uploaded to 3D printer software, resulting in conversion from the digital object to a physical equivalent.
Essentially, it’s an enabler for the core suite of Industry 4.0 technologies — such as cloud computing, smart automation, IoT devices, digital inventory, and data analytics — to be directly applied to the process of fabrication itself. While previously this was only applicable to select, less demanding applications, the expansion of professional 3D printer technologies — such as broadened material offerings in both composites and metals, as well as substantial improvements to speed, reliability, accuracy, and quality — allow it to comfortably digitize manufacturing processes for a far wider breadth of applications, and on a larger scale than before. In a way, 3D printing is the specific technology most emblematic of Industry 4.0: amongst the list of individual technologies that collectively shape it, 3D printing is the only one that holistically applies the defining characteristics to the actual fabrication of parts.
While the capabilities of professional 3D printers have helped shape Industry 4.0, many Industry 4.0 technologies have also fueled the growth of additive manufacturing. When first introduced, professional 3D printers were naught but individual hardware items. Additive manufacturing has since grown with Industry 4.0, into today’s full-fledged 3D printing platforms with advanced 3D printing software capabilities, connectivity to devices in disparate geographical locations, a wide range of advanced analytics, and AI-driven automated features such as autonomous part inspection.
Examples of How 3D Printers Use Industry 4.0 Technologies
To enable manufacturers to get the most out of each professional 3D printer, additive manufacturing solution providers have integrated the core set of Industry 4.0 technologies into their 3D printer platforms.
Here are examples of the technologies, how they augment professional 3D printers, and how they solve problems for manufacturers:
Cloud computing provides connectivity between users and every professional 3D printer operated by an organization, across disparate geographic locations. Effectively, a user can hop on their laptop and initiate printing of a repair part for a factory halfway across the globe.
With a digital inventory of parts as data items stored in the cloud, this ability confers numerous benefits: manufacturers can avoid the need to stock up on large amounts of inventory, and effectively operate with a lean manufacturing model with just-in-time (JIT) production. Furthermore, a distributed manufacturing model allows users to avoid supply chain complications and simply get parts faster, by printing parts to the exact point of need when they are needed, as opposed to submitting an order for a part to be created at one location and having it shipped to the point of need.
Software for today’s professional 3D printers also provide various data analytics for their users. Organizations can track metrics such as material usage, print job quantities per user according to time intervals, printer bandwidth per user, parts uploaded per week, and custom analytics fields. Print times and costs per print job are calculated according to variables such as part size, material, and volume of fiber used to reinforce the plastic matrix. Using these analytics can allow organizations to understand usage patterns of equipment and optimize resources accordingly.
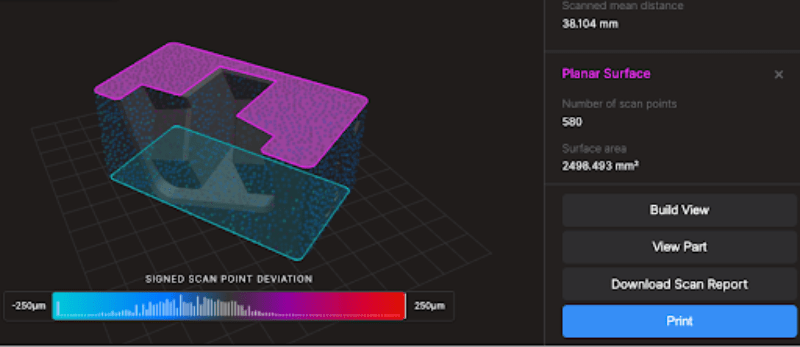
Professional 3D printers are inherently automated by nature — simply hitting the “print” button will take you from art to part in just hours to days without the need for hands-on work, management, or human oversight. With in-house additive manufacturing, engineers do not have to worry about time-consuming procurement activities like drafting drawings, submitting purchase orders, and managing the bidding process with multiple vendors.
More recently, quality inspection of parts has been fully automated — during the fabrication process, AI-powered 3D printing software can verify that a printed part is immediately usable in the factory, automatically generating part quality and traceability reports.
Through 3D printing software APIs, professional 3D printers can also integrate with other core systems within a smart factory, such as through a Manufacturing Execution System (MES), Enterprise Resource Planning (ERP) or Enterprise Asset Management (EAM) system. Print jobs can be initiated through any of these systems. If a user requests a part in one of these systems, that system can trigger an automatic print job in any specific 3D printer.
What Does This Mean for Manufacturers?
Through the integration of Industry 4.0 technologies, AM has allowed manufacturers to connect their manufacturing across geographic locations, enable a lean manufacturing model with the accessibility of a digital inventory, and automate a lot of the arduous tasks that come with part fabrication.
As professional 3D printer technologies continue to develop, digitization through Industry 4.0 technologies can be expected to reach an even wider range of digital manufacturing applications.
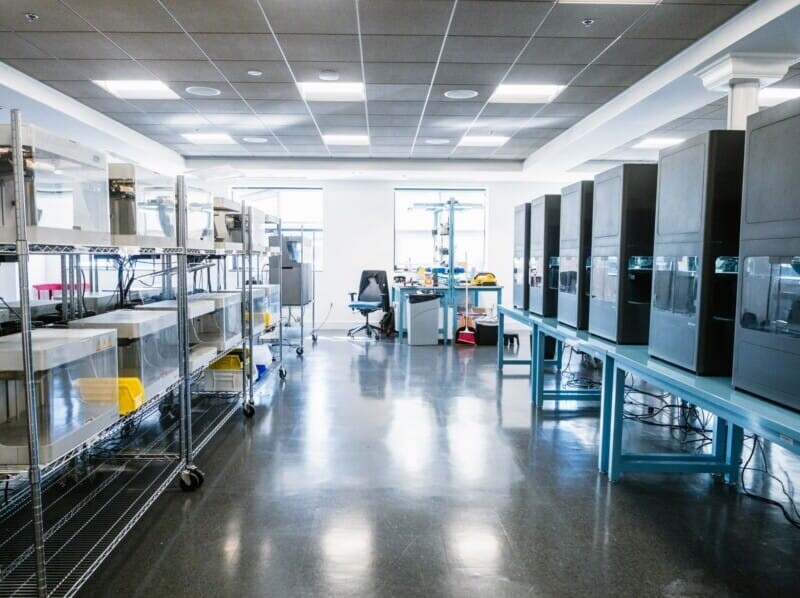
Additive Manufacturing History: From the 1980's to Now
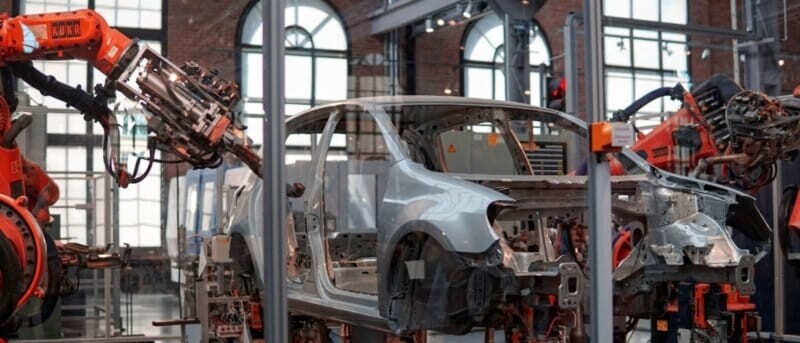
Factories of the Future: Powered by 3D Printers and High Performance Materials
All of the blogs and the information contained within those blogs are copyright by Markforged, Inc. and may not be copied, modified, or adopted in any way without our written permission. Our blogs may contain our service marks or trademarks, as well as of those our affiliates. Your use of our blogs does not constitute any right or license for you to use our service marks or trademarks without our prior permission. Markforged Information provided in our blogs should not be considered professional advice. We are under no obligation to update or revise blogs based on new information, subsequent events, or otherwise.
Never miss an article
Subscribe to get new Markforged content in your inbox