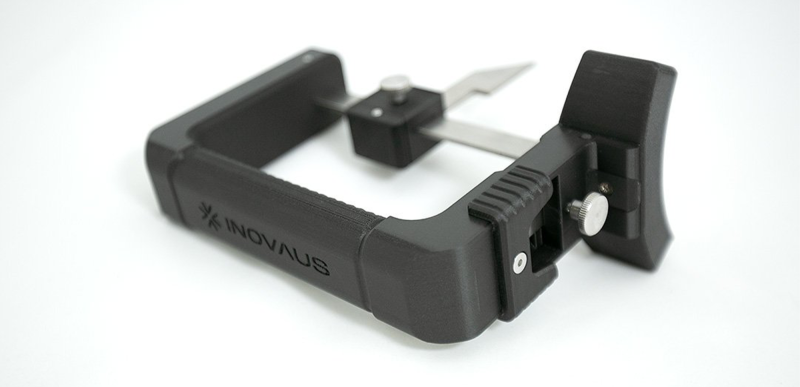
CADDS Group - Calibro per ingranaggio di traino
Il Gruppo CADDS, con sede nell'Australia Occidentale, impiega oltre 180 dipendenti in sei divisioni Rilievo, Progettazione tecnica, Progettazione di prodotto, Progettazione edilizia, Progettazione ambientale sostenibile e Fabbricazione. Ogni divisione copre un'ampia gamma di servizi per alcune delle più grandi aziende dello Stato. L'elenco dei clienti del settore minerario include aziende quotate come Rio Tinto, BHP, Alcoa e CSIRO, l'agenzia governativa australiana responsabile della ricerca scientifica.
Nel 2023 il Gruppo CADDS ha rafforzato strategicamente le proprie capacità con un investimento in tre stampanti Markforged all'avanguardia: FX20™, Mark Two™ e Metal X™. Queste attrezzature avanzate, ha spiegato l'amministratore delegato Darren Clark, consentono al Gruppo di fabbricare parti e attrezzature con un'elevata resistenza e una precisione senza pari. Utilizzando materiali avanzati come la fibra di carbonio continua, l'acciaio inossidabile, il rame e gli acciai per utensili, la tecnologia spinge le loro attività all'avanguardia dell'innovazione.
Norbert Babooram, Product Design Manager di Inovaus, la divisione per la progettazione dei prodotti del Gruppo CADDS, ha dichiarato che l'accesso alle strutture di stampa interne consente al suo team di ideare soluzioni più rapide ed efficienti per le sfide dei clienti.
"Quando abbiamo acquisito le nostre stampanti, uno dei nostri principali clienti di un'azienda mineraria ci ha invitato a partecipare alla progettazione di un nuovo dispositivo per misurare l'usura di tutti gli ingranaggi di traino dei vagoni ferroviari", ha dichiarato Norbert.
L'attuale metodo di misurazione prevede l'uso di un metro a nastro e di un righello e implica la rimozione dell'ingranaggio di traino dall'accoppiamento del carro, con un basso livello di accuratezza e un processo che richiede molto tempo e che, in ultima analisi, fa lievitare i costi. Come ha sottolineato Norbert, l'ingranaggio testato è spesso entro i limiti di usura, quindi è stato rimosso inutilmente, a causa di letture imprecise.
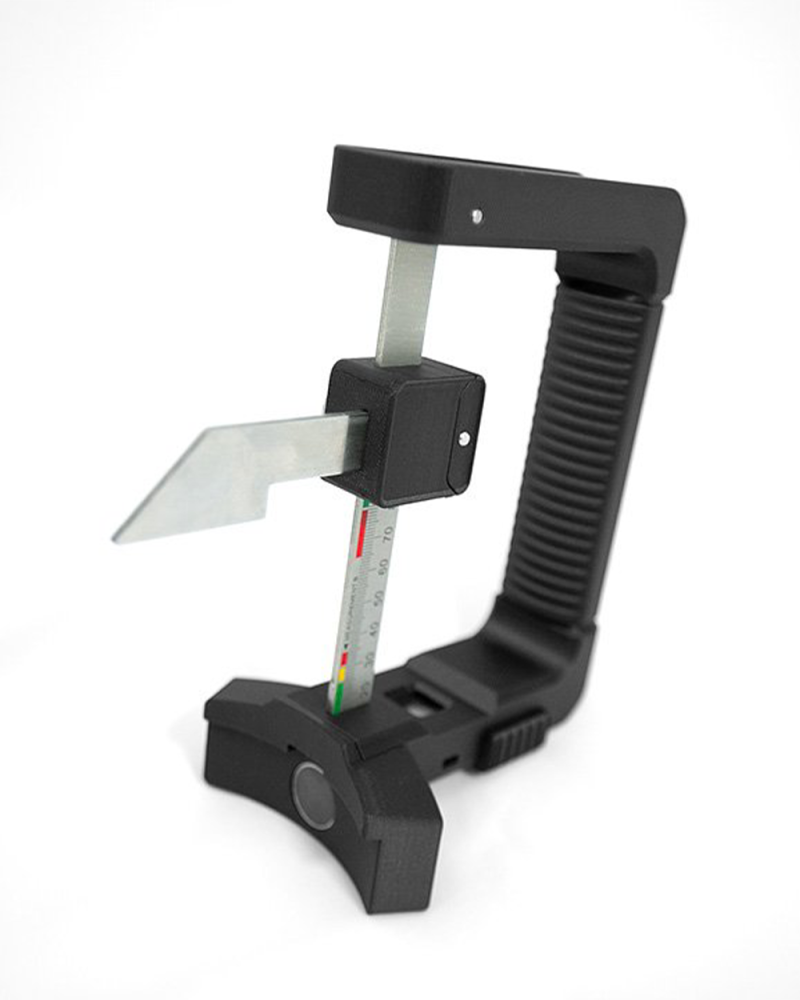
"Il cliente aveva prodotto un progetto di massima per un nuovo calibro, che richiedeva tre diversi dispositivi per diverse parti del processo di misura; nel giro di una settimana siamo stati in grado di elaborare un progetto per un unico dispositivo in grado di eseguire l'intero processo di misura", ha dichiarato Norbert.
Nel giro di una notte, un prototipo è stato stampato sulla Mark Two, testato su un ingranaggio di traino presso la sede di Inovaus, e prontamente spedito al cliente per la valutazione. Il feedback è stato entusiastico e il prototipo è stato utilizzato più volte in loco.
"Abbiamo progettato e stampato una seconda versione, che il cliente ha approvato e utilizzato in loco. In pochi giorni siamo riusciti a progettare altri elementi e a stampare un dispositivo in grado di misurare l'ingranaggio mentre è ancora in posizione nell'accoppiamento del carro", ha dichiarato Norbert.
Ogni versione progettata da Inovaus è modulare, quindi le singole parti possono essere modificate senza dover rivedere l'intero dispositivo, e le sezioni su misura possono essere progettate per adattarsi a diversi tipi di ingranaggi.
Il team di Norbert ha calcolato i costi di progettazione e produzione in base allo stampaggio a iniezione e ha stimato che l'intero processo, compreso lo sviluppo e la produzione dello stampo, avrebbe richiesto almeno 500 ore. Progettata in appena una settimana, la versione realizzata con la produzione additiva può essere stampata durante la notte a un costo pari all'1,5% del costo complessivo dello stampaggio a iniezione.
"Il calibro ha un potenziale internazionale immenso. La progettazione e la produzione di questi primi modelli fornisce una prova tecnica e ci permette di essere presenti sul mercato per far conoscere il prodotto. Questo non sarebbe stato possibile senza la produzione additiva", ha dichiarato Norbert.
Le stampanti 3D industriali di Markforged offrono importanti vantaggi all'industria mineraria grazie all'esclusivo ecosistema Digital Forge, che rende possibile il funzionamento, la gestione e il monitoraggio a distanza dai siti minerari. Questa tecnologia permetterà al Gruppo CADDS di produrre parti ad alte prestazioni e componentistica in loco, riducendo i tempi di consegna, minimizzando i tempi di inattività e migliorando l'efficienza operativa complessiva.
– Norbert Babooram Product Design Manager, Inovaus“La versione realizzata con la produzione additiva può essere stampata durante la notte a un costo pari all'1,5% del costo complessivo dello stampaggio a iniezione."
All of the blogs and the information contained within those blogs are copyright by Markforged, Inc. and may not be copied, modified, or adopted in any way without our written permission. Our blogs may contain our service marks or trademarks, as well as of those our affiliates. Your use of our blogs does not constitute any right or license for you to use our service marks or trademarks without our prior permission. Markforged Information provided in our blogs should not be considered professional advice. We are under no obligation to update or revise blogs based on new information, subsequent events, or otherwise.
Never miss an article
Subscribe to get new Markforged content in your inbox