Fiber appears in 3D printed parts in two different formats, and it’s important to understand the distinction.
Chopped fibers less than a millimeter long are suspended in a nylon base thermoplastic. This combination, called a filled plastic, is extruded using a standard FDM printing process. These chopped fibers augment the plastic, increasing yield stress and flexural strength (which you can find on our datasheet). This combination of nylon and chopped carbon fiber is not technically a composite because the fibers are blended inside the plastic, rather than remaining distinct.
Continuous fibers, including fiberglass, carbon fiber, and Kevlar, are what endow a composite part with the directional strength of metal. They have elastic moduli between 16 times and 46 times greater than those of plastics, with carbon fiber’s being almost equivalent to aluminum’s (60 GPa and 69 GPa, respectively). As opposed to chopped fibers being suspended in the plastic, continuous fibers run uninterrupted through a part, thus distributing the load across the three-dimensional geometry. They perform best in tension, so it is critically important to print them with loading conditions in mind.
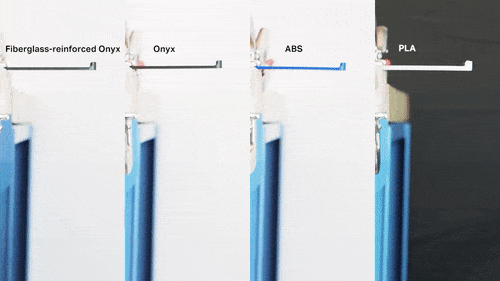
Because of their distinct properties, fibers require a different 3D printing method from FDM. They are not melted and extruded like plastic, but instead are laid down intact through a secondary print nozzle. As this happens, a thin plastic coating around the fiber melts so that they adhere to the matrix. This type of composite-building is called Continuous Fiber Fabrication (CFF), and it is unique to Markforged printers.
How does the printer know where to put fiber? All compositing parameters are defined in Markforged’s slicing software, Eiger. After the user has indicated which layers get fiber, how much, and in what pattern, the software instructs the printer to place solid-infill “floor” layers above and below the region which includes fiber, as well as when to switch between plastic infill and continuous fiber routing.
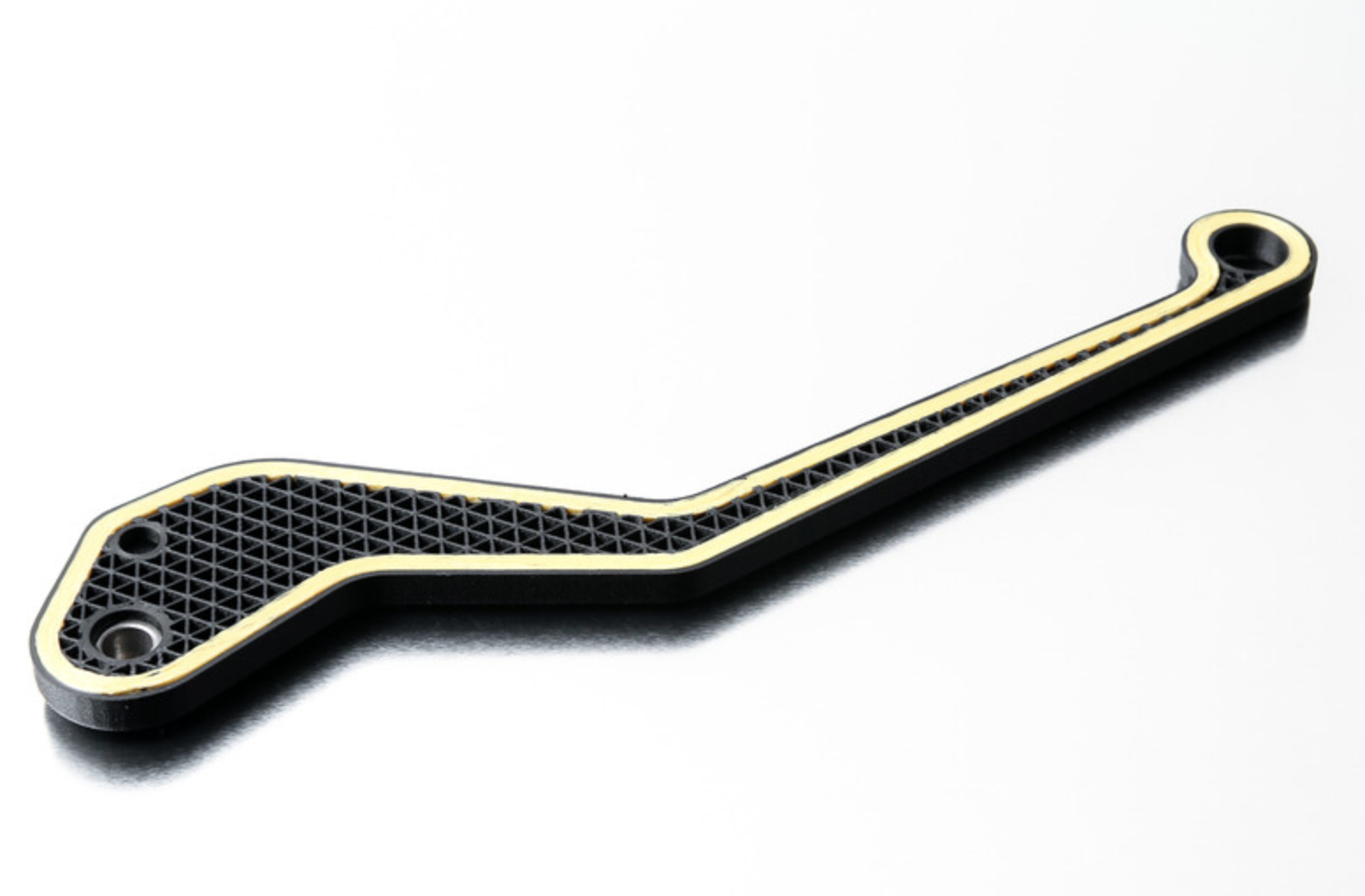
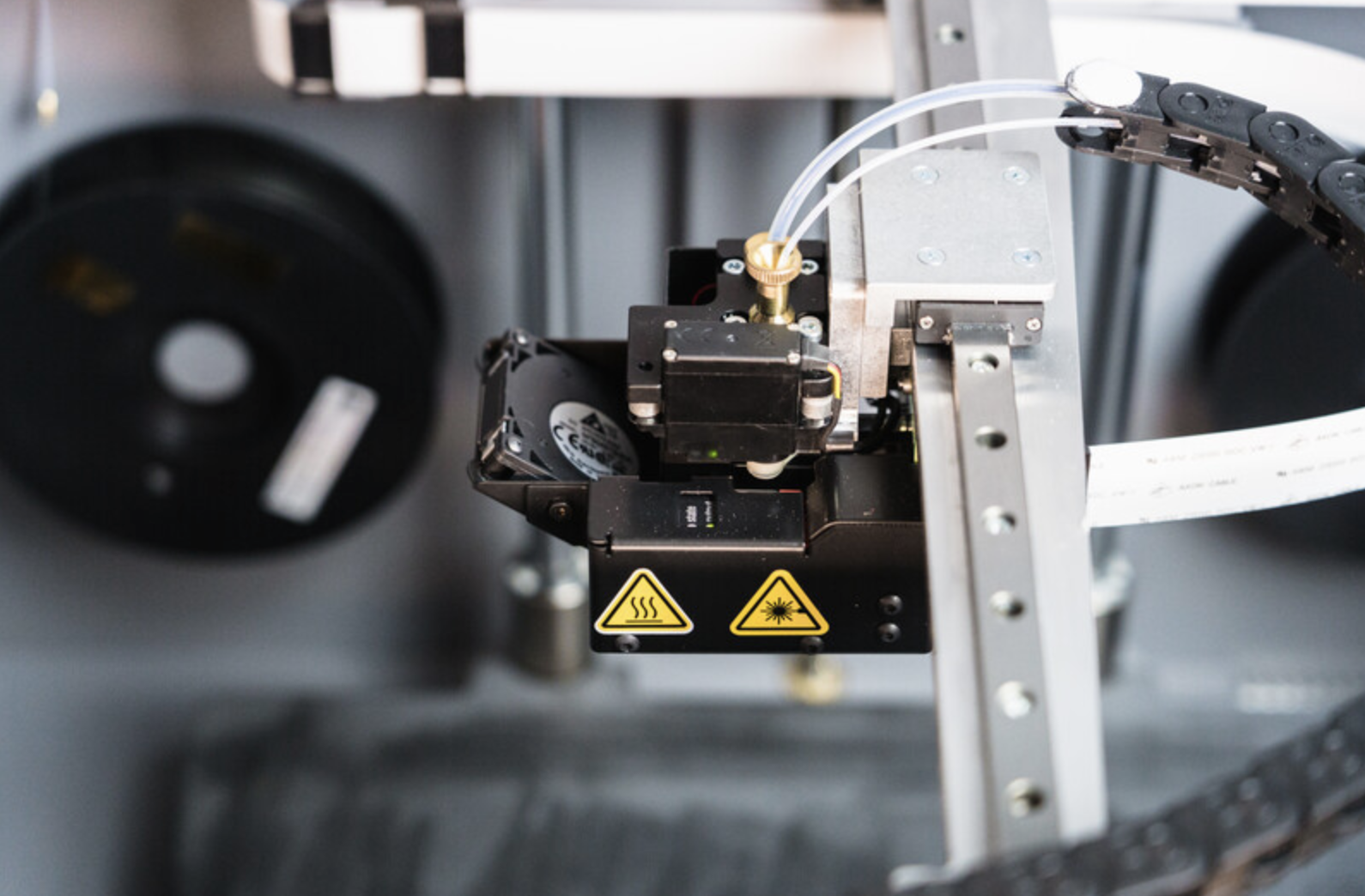
The ability of the printer to integrate user-defined fiber patterns layer-by layer is what makes this fabrication process so exceptional. Composites themselves as an engineering strategy may not be new, but what is fundamentally different now is the ease with which they can be implemented as functional alternatives to metal parts.
Three Matrix Plastics, Four Continuous Fibers
As the printer user, you have options: choose from three plastics — Nylon, Onyx, Onyx FR — and four fibers — fiberglass, carbon fiber, Kevlar, and high-strength-high-temperature (HSHT) fiberglass — to optimize your part for loading and work environment. These 15 combinations (including the option without fiber) make for a versatile printer capable of delivering a wide range of part properties.
Need brute strength combined with flame retardance? Use Onyx FR and carbon fiber. Want to handle repeated loading and show a smooth white finish? Try Nylon and Kevlar. How about any robust yet inexpensive consumable part? Combine Onyx and fiberglass. Below is a brief overview of the four fiber materials and three matrix options, so you know when to use each. Explore more about these on the materials page, composites datasheet, and fiber datasheet.
Plastics
Nylon White is smooth, non-abrasive, and easily painted. It can be reinforced with any continuous fiber and works best for non-marring work holding, repeated handling, and cosmetic parts. It is far stronger than PLA, and nearly as strong as ABS.
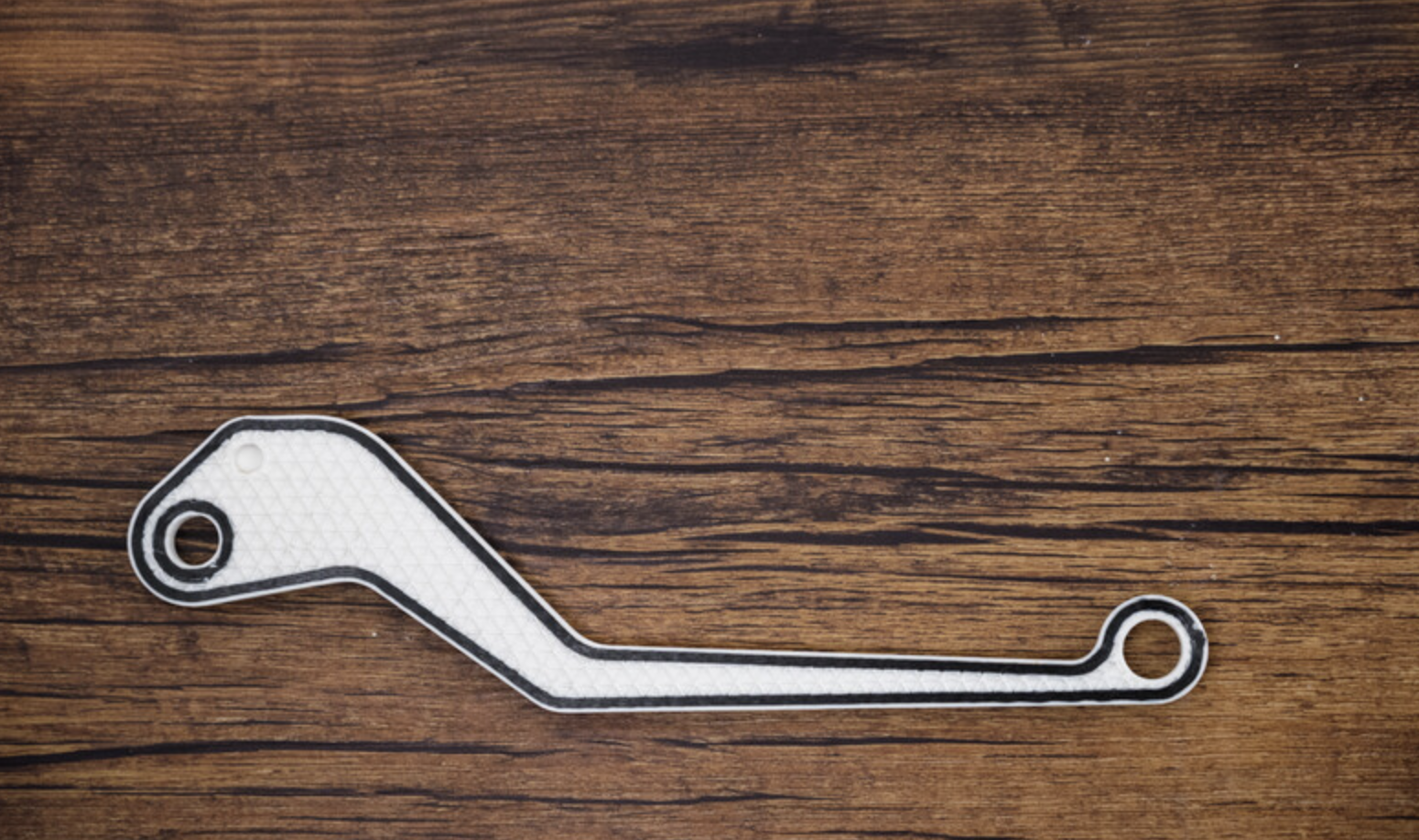
Onyx is the chopped carbon fiber reinforced nylon, discussed above. It’s 1.4 times stronger and stiffer than ABS and can be reinforced with any continuous fiber. Onyx sets the bar for surface finish, chemical resistivity, and heat tolerance.
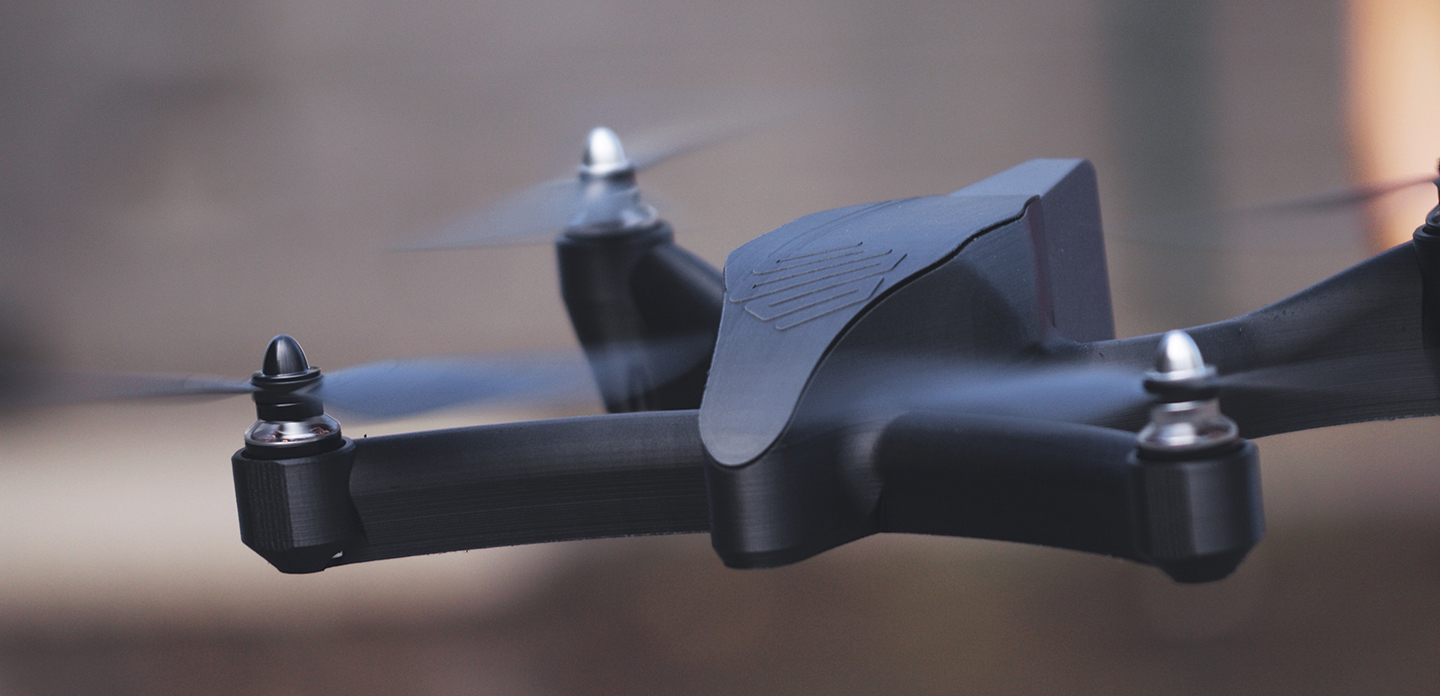
Onyx FR achieves V-0 rating on the UL94 flammability test while possessing similar mechanical properties to Onyx. It’s best for applications in which flame retardancy, minimal weight, and strength are required.
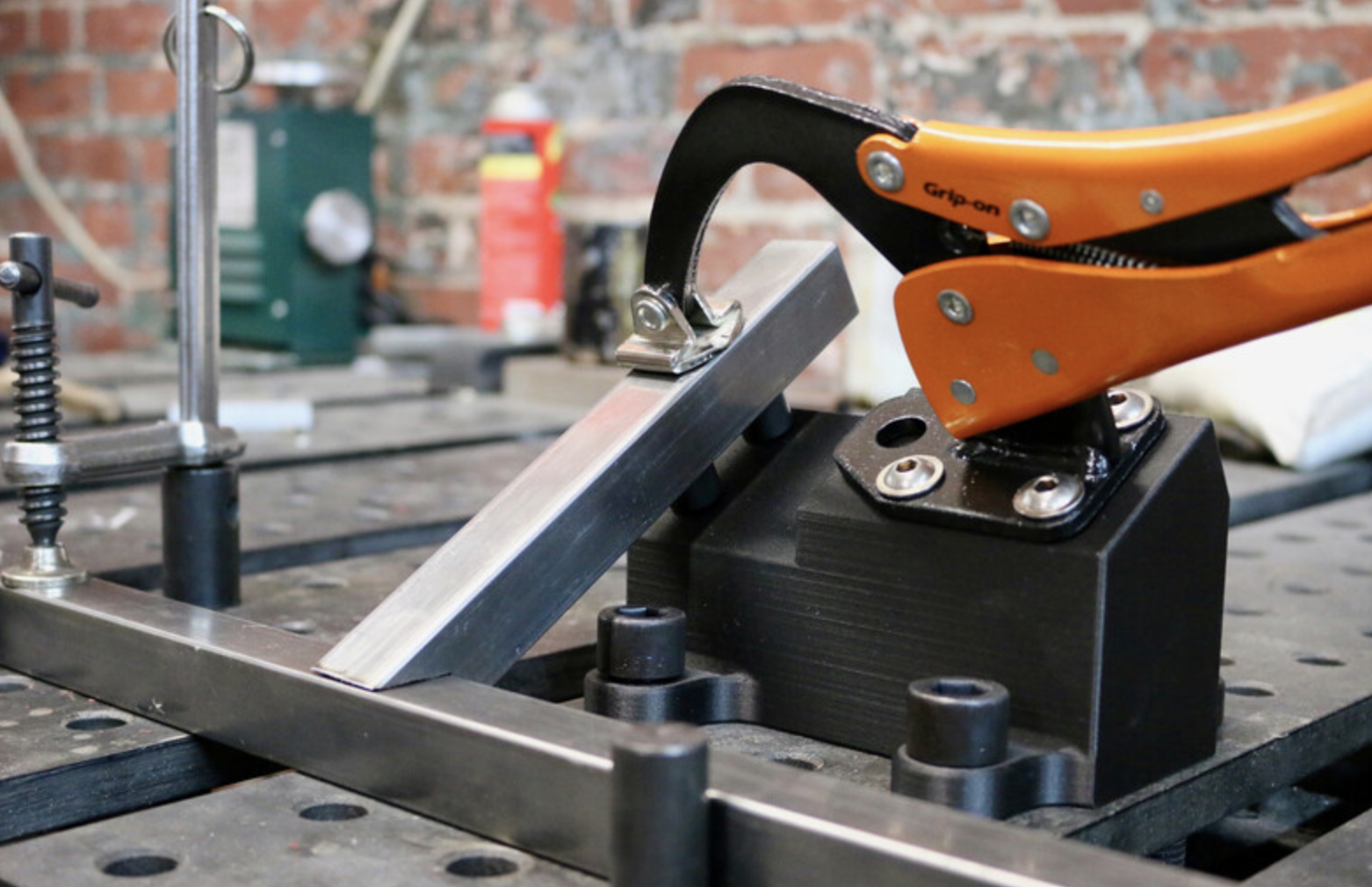
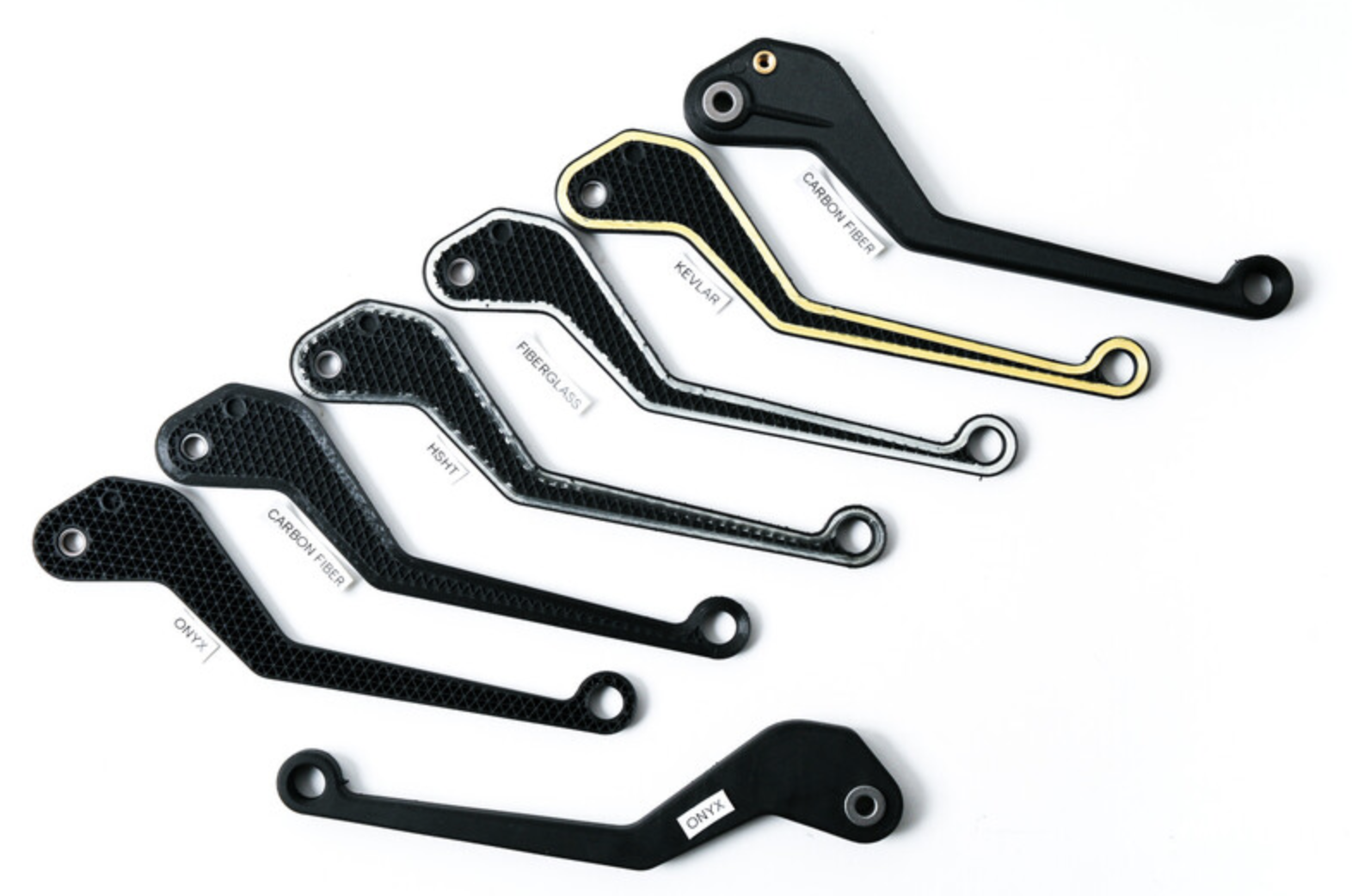
Fibers
Fiberglass is the all-purpose fiber: it works in most scenarios, and is the cheapest Markforged fiber option. Fiberglass is 3 times stronger and 11 times stiffer than ABS, and performs best under intermittent loading. Its most common applications include works-like prototypes, brackets, drill jigs, and soft jaws.
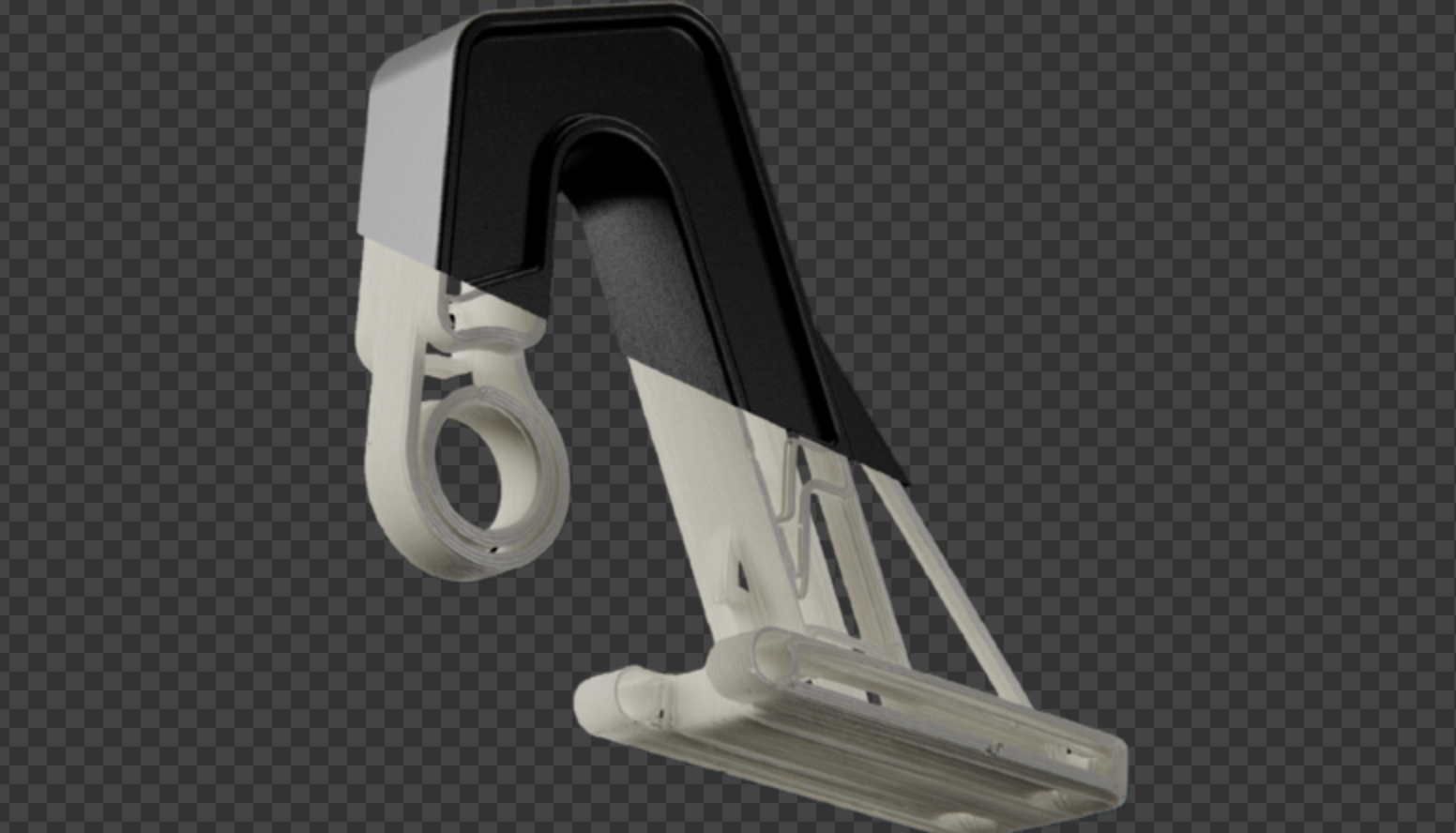
Carbon fiber is the workhorse of the four fibers, boasting a strength-to-weight ratio 50% better than 6061 aluminum, a tensile modulus roughly equivalent to that of aluminum, and a stiffness 24 times that of ABS. If maximal strength is what you need, carbon fiber is the best option. Markforged customers replace machined aluminum parts with carbon fiber-reinforced Onyx — which can be easily tweaked between prints, with no machinists required. Its applications include inspection fixtures, machining fixtures, cantilevered members — e.g. in a robotic arm — and any end-use parts that are subject to constant loading.
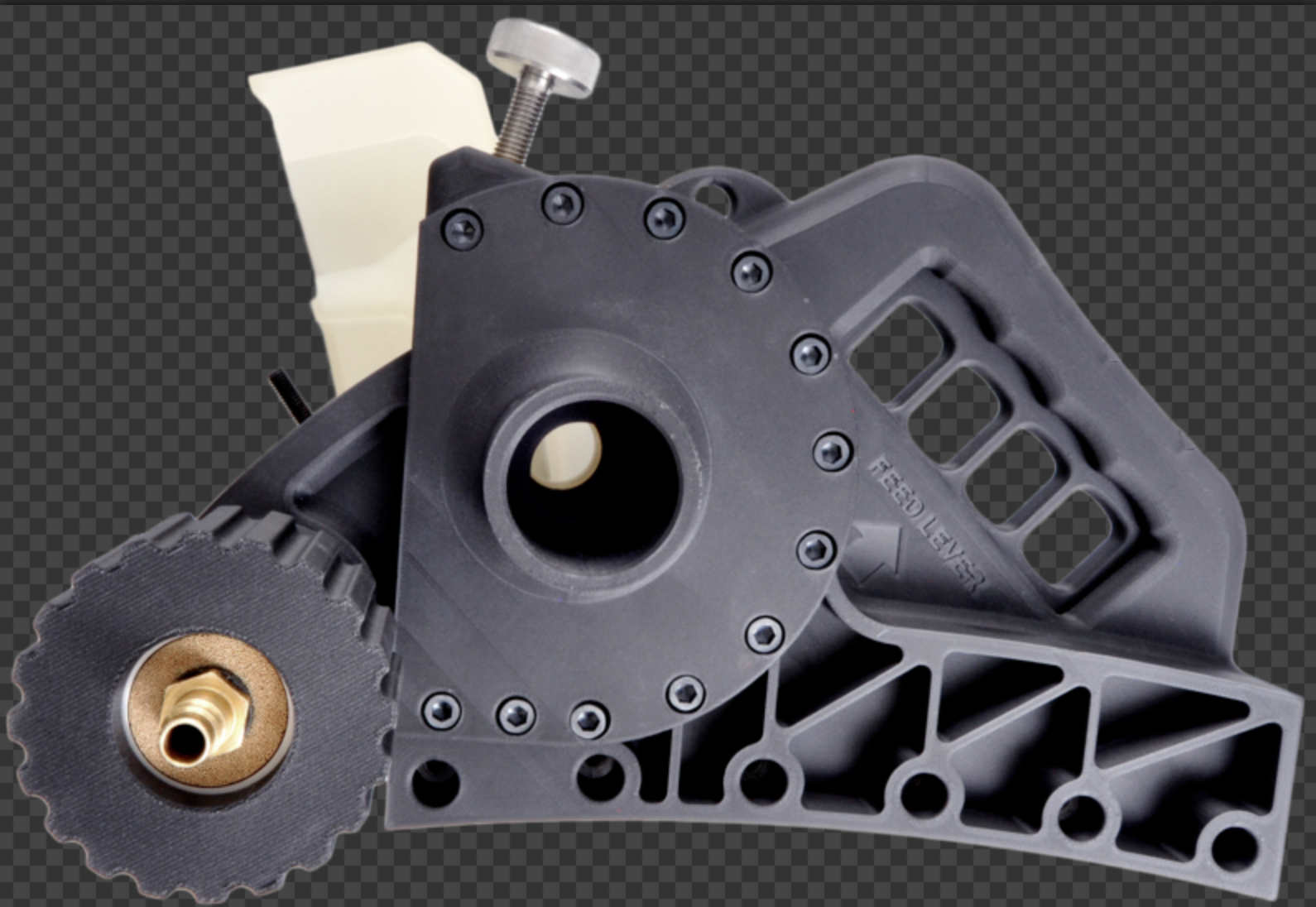
Kevlar is extremely durable and shock resistant, and will elastically deform much farther prior to failure than other fibers. Ideal applications include any repeated or sudden impact, such as clamping or stamping, or wherever advance warning of failure is preferred.
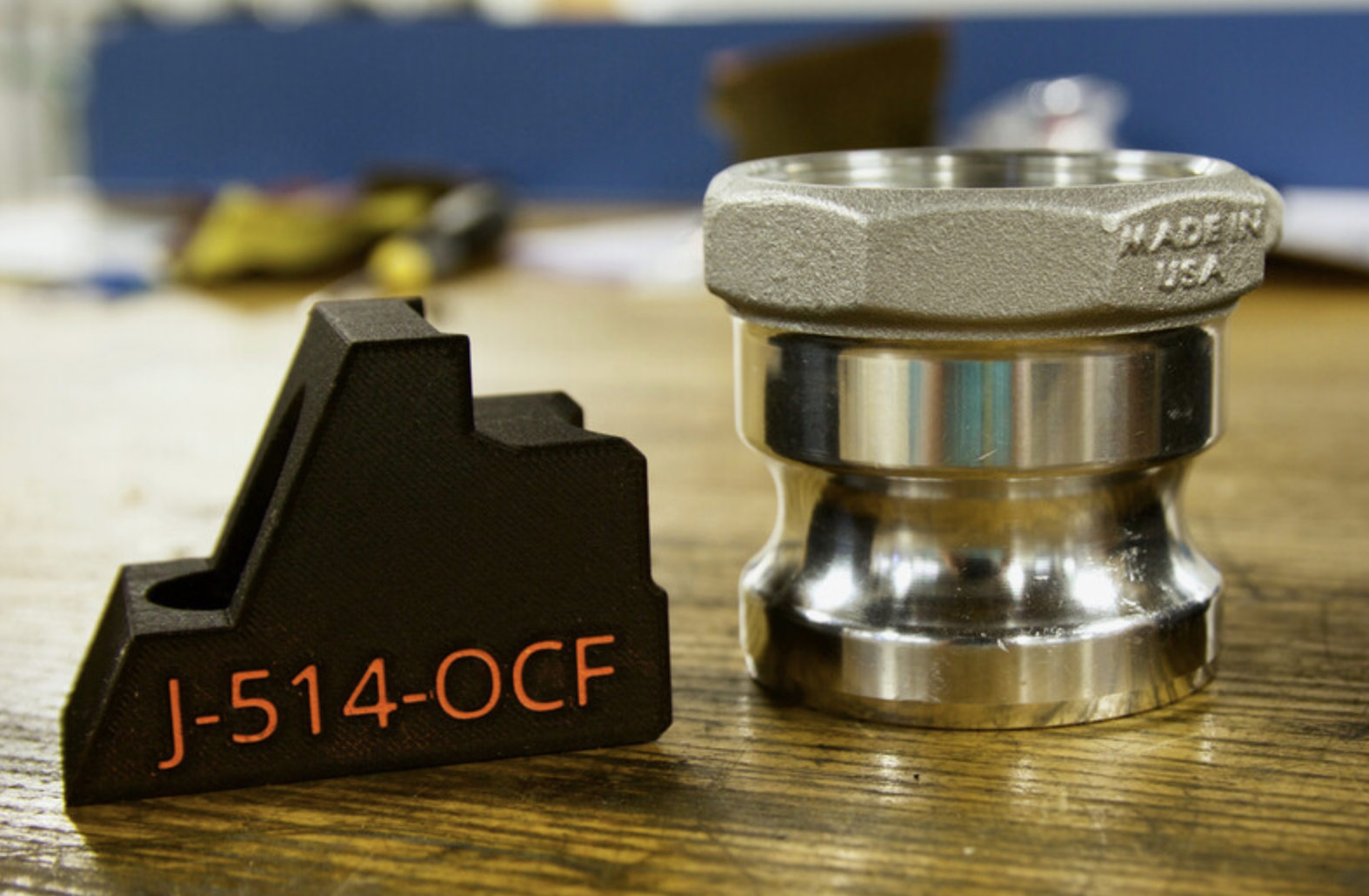
HSHT fiberglass maintains its material properties up to 150°C or even 200°C, rather than 105°C for other fibers. That means it is less susceptible to thermal effects and will stay strong even when other fibers elongate from heat (this is true for HSHT even in composite form because Onyx and Onyx FR follow closely at 145°C heat deflection). HSHT is suitable for both constant and intermittent loading, and common applications include weld fixtures, thermoforms, thermoset molds, and blow molds.
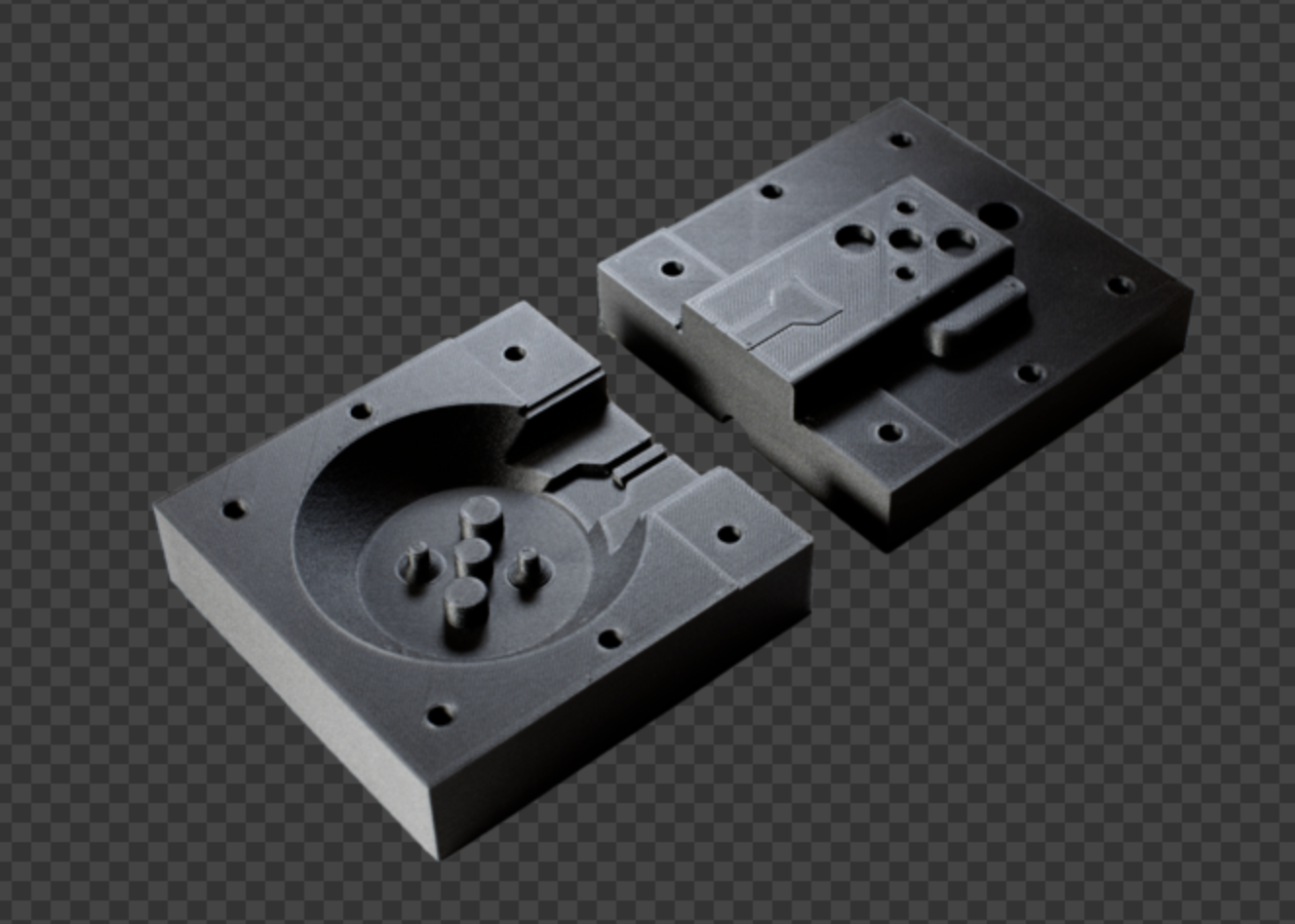
There is a wide overlap in use cases for all fibers. Reinforcing a plastic matrix with any fiber will offer huge benefit, given that all fibers are far stronger than plastic alone, and each fiber is further optimized for specific loading scenarios. While only one kind of fiber may be incorporated into a given part, you can control where you put the fiber to adjust your part's performance. You can visualize these traits in the diagram below.
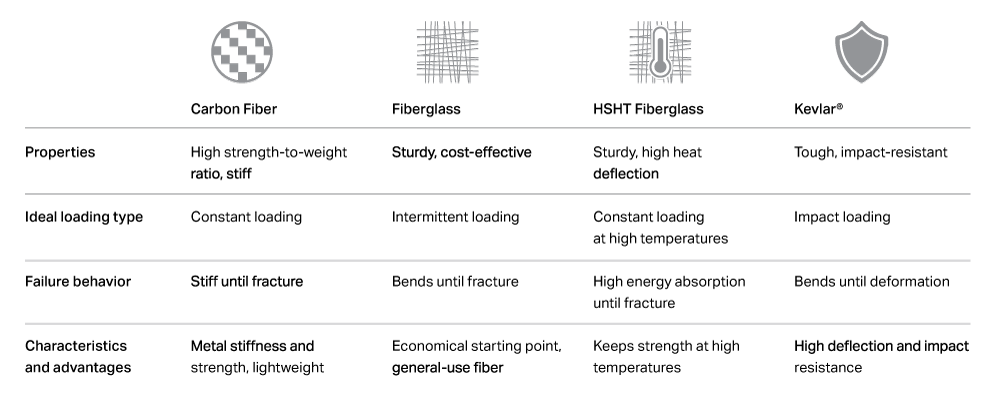
So, how do you choose which material is best for your part’s function, and how do you implement your fiber reinforcement strategy in the slicing software? Read our article on Beam Bending Theory for an in-depth explanation of how continuous fiber impacts part strength, or continue to the next section where we break down how to print a functional composite part.