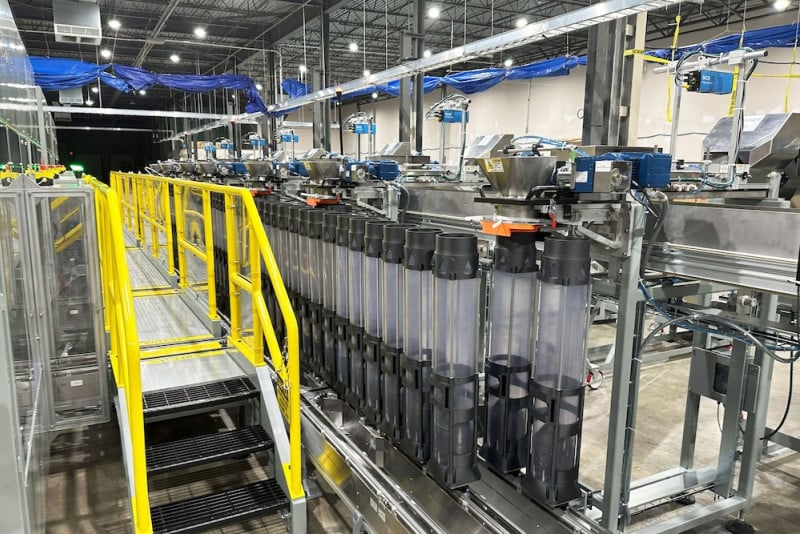
Enhancing Packaging Machine Builders' Efficiency with Custom Additive Manufacturing Solutions
The food packaging industry is undergoing rapid transformation, driven by evolving consumer demands, sustainability goals, and the need for cost reduction. Packaging machine builders must adapt quickly to these changes, ensuring their machines can handle the new requirements without sacrificing performance or increasing costs. Custom additive manufacturing (AM) solutions are emerging as a powerful tool to meet these challenges, offering flexibility, cost-effectiveness, and speed that traditional manufacturing methods can’t match.
Challenges facing the Packaging Industry in 2024 and beyond
Innovation and rapid changes in consumer behavior are pushing food and beverage companies to adapt their packaging lines to meet new demands — whether it’s a shift toward bulk buying, the preference for sustainable packaging, or the need for rapid product changeovers. Packaging machine builders, in turn, must develop machines that are not only versatile but also capable of quick adjustments to accommodate these trends.
Farason Corporation faced the challenge of moving heavy, irregularly shaped shampoo bottles on a fast-moving production line. Traditional off-the-shelf packaging solutions couldn’t meet the required payload limits for their robot, which led to slower cycle rates and reduced productivity. By adopting custom AM solutions, Farason was able to develop a lightweight, high-performance End of Arm Tooling (EOAT) that met the demands of their production line, enabling them to maintain high speeds and improve overall efficiency.
Why Additive Manufacturing Matters
Additive manufacturing, commonly known as 3D printing, is the process of creating objects by adding material layer by layer. In the packaging industry, where each product might require unique handling and packaging solutions, the ability to quickly and affordably produce custom parts for the manufacturing line is invaluable.
Farason Corporation leveraged AM to create a custom quick-change mount plate for a vacuum gripper EOAT. Traditional manufacturing methods would have required costly and time-consuming milling processes, resulting in a heavier part that would have compromised the robot’s performance. With AM, they produced a lightweight, robust part that not only met their immediate needs but also allowed for easy future modifications.
Comparing Additive Manufacturing vs Traditional Solutions for Machine Builders
Traditional manufacturing often involves lengthy lead times, high costs, and limited design flexibility. In contrast, AM offers fast production of affordable, high-performance parts that can be tailored to specific applications, from development and production to maintenance.
Suntory Products Limited implemented Markforged 3D printers to produce precise, high-strength parts for their packaging process. The Haruna plant, where these printers were first introduced, significantly reduced the time and cost associated with outsourcing custom parts. The engineers were able to design and produce jigs and covers in-house, ensuring that each component met their exact specifications and could be produced on-demand.
Formulating solutions to address the rapidly multiplying SKUs and frequently refreshed packaging now common to the food manufacturing industry can be a frustrating challenge for manufacturing teams. How can teams squeeze more performance and agility out of each line when the equipment used last month isn’t compatible with the packaging of the version launching next month? How can faster changeovers be accomplished to meet mixed packaging and demand-driven supply chain agility?
Production-ready additively manufactured (AM) end-of-arm tooling (EOAT) offers a solution by enabling teams to consolidate and customize end-effector solutions while also reducing costs and lead times. For example, with Markforged’s industrial 3D printers, manufacturing teams can fabricate strong parts on-demand at the point of need, bypassing the long development cycles and high costs typically associated with conventional custom part machining.
A key advantage of AM is the ability to modify designs with lightweight material while maintaining metal-like strength through continuous fiber reinforcement. This allows for further customization, including the integration of additional functionalities such as vacuum systems, sensor mounting, and cable routing directly into the design of parts. By incorporating these elements, the risk of entanglement or collision with other parts of the work environment is minimized, which ultimately reduces potential downtime.
Moreover, the lightweight nature of these parts makes them compatible with smaller robots, enabling manufacturing teams to deploy an automation module at any position on the line using a collaborative robot. The flexibility offered by Markforged’s Digital Forge™ allows teams to keep production lines running smoothly by producing the custom parts they need right on the factory floor.
A practical example of this is the design process for a suction gripper used in the final packaging step to transport unit containers into retail packaging boxes. The distance between grips often depends on the latest product and box shape, and by utilizing AM, the manufacturing team can adjust the length on the fly to suit the latest requirement while minimizing weight.. Fabricating the part in-house eliminates delays caused by waiting for a supplier to ship a custom part. The use of Onyx, a micro-carbon fiber-filled nylon, allows for faster production of parts, lowers total costs, and decreases the weight—and thus the load—on the packaging robot.
Solving Major Pain Points
One of the significant pain points in the packaging industry is the high cost and long lead times associated with outsourcing custom parts. Additionally, managing multiple vendors and dealing with the incompatibility of parts can lead to inefficiencies and increased operational costs.
Farason Corporation encountered this issue when they needed custom EOAT components that were both lightweight and durable. By using AM, they were able to produce these parts in-house, reducing lead times from weeks to hours and cutting costs significantly. This approach also allowed them to maintain consistent quality across multiple machines, ensuring that any replacement parts would match the original specifications exactly.
The positive outcomes AM can drive on the factory floor
Increase Machine Performance and Reduce Cost
Additive manufacturing enables rapid prototyping and the production of customized parts, which can significantly enhance machine performance while reducing costs. By eliminating the need for expensive tooling and outsourcing, companies can optimize their machine designs and reduce overall production costs.
In the case of Farason Corporation, using Markforged’s industrial 3D printers allowed them to produce high-performance EOAT parts at a fraction of the cost of traditional methods. The ability to quickly iterate and modify designs also meant that they could handle more projects without straining their resources, ultimately delivering better results to their clients faster.
Reduce Time to Market
One of the key advantages of AM is the ability to shorten development cycles, allowing machine builders to bring new products to market faster. The flexibility of AM also means that teams can handle more projects simultaneously, without compromising on quality or delivery times.
Suntory Products Limited experienced this firsthand at their Haruna plant. By using AM to produce jigs and other custom components, they were able to reduce the time needed for product switchovers and maintenance, allowing them to keep their production lines running smoothly and efficiently.
Deliver Spares and Upgrades Cheaper and Faster
On-demand part production is one of the most significant benefits of AM, particularly when it comes to delivering spare parts and upgrades. With AM, machine builders can reduce both costs and lead times, ensuring that their customers receive the parts they need quickly and affordably.
At Suntory Products Limited, the use of Markforged 3D printers allowed the Haruna plant to produce nearly 900 parts in just over 8,000 hours, significantly reducing downtime and maintenance costs. The ability to create custom jigs and covers in-house also meant that they could easily adapt to new production requirements without waiting for parts to be shipped from external suppliers.
Common Applications for Packaging Machinery
Custom additive manufacturing solutions are particularly well-suited for packaging machinery applications, where precise, high-performance parts are required. Some common applications include:
End-of-arm tooling/grippers: Custom EOAT, like those developed by Farason Corporation, can be tailored to specific products, ensuring optimal performance and reducing downtime. Farason used additive manufacturing to develop a mechanical gripper with a custom collar for robotics packaging automation.
Cable/hose management: Farason Corporation also used AM to create custom hose clamps for a robotic arm, ensuring that the hoses remained securely in place during complex multi-axis movements.
Mounts and brackets: AM allows for the production of custom mounts and brackets that can be easily integrated into existing machinery, improving overall performance and reducing the need for costly modifications.
Changeover components: Custom AM parts can be quickly produced to facilitate faster changeovers, reducing downtime and increasing overall efficiency.
Custom collection/transport solutions: Farason Corporation leveraged Markforged 3D printers to create custom small package containers for a prominent snack food company, addressing challenges that traditional methods couldn’t solve. By using additive manufacturing, they designed and produced affordable, lightweight, and functional containers in-house, which enabled them to win the bid and optimize the solution for deployment. This application highlights the ability of 3D printing to deliver cost-effective, tailor-made solutions in the packaging industry.
Conclusion
Custom additive manufacturing offers packaging machine builders a powerful tool to enhance efficiency, reduce costs, and accelerate time to market. By adopting AM solutions, companies can address the challenges of an evolving industry, ensuring that their machines remain competitive and capable of meeting the demands of today’s consumers. With the ability to produce high-performance parts quickly and affordably, AM is set to become an integral part of the packaging industry’s future.
All of the blogs and the information contained within those blogs are copyright by Markforged, Inc. and may not be copied, modified, or adopted in any way without our written permission. Our blogs may contain our service marks or trademarks, as well as of those our affiliates. Your use of our blogs does not constitute any right or license for you to use our service marks or trademarks without our prior permission. Markforged Information provided in our blogs should not be considered professional advice. We are under no obligation to update or revise blogs based on new information, subsequent events, or otherwise.
Never miss an article
Subscribe to get new Markforged content in your inbox