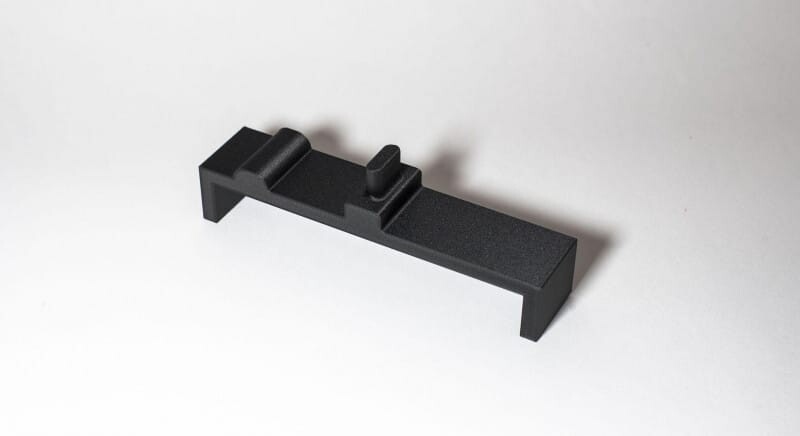
3D Printing Assembly Fixtures with Markforged Composites
One of the most prevalent challenges for manufacturing engineers is keeping up with fabrication of product line tooling. Creating fixturing, tooling, and jigs are essential for operators and technicians to safely and efficiently carry out day-to-day production in a work cell. Whether it’s a CMM fixture for in-line inspection, soft jaws for holding a workpiece, or an assembly fixture for joining subcomponents, the value that custom tooling provides is ubiquitous.
Fabricating assembly fixtures is typically extremely taxing on a tool room. Without even considering the time spent in engineering design, the production of an assembly fixture with traditional manufacturing methods is extremely costly, time-consuming, and labor-intensive. Teams need to leverage mills, lathes, cutting operations, drilling, and routers to create an assortment of fixtures. Using machining operations are not only very expensive from a capital expense and industrial process side, though — in most environments — are the same equipment used to make a customer’s parts. It’s also rare that an assembly fixture comes out perfect the first time. Doing iterations is an assumed part of the industrial design process, but the result is a multiplication of the time and cost per each attempt at making the perfect fixture.
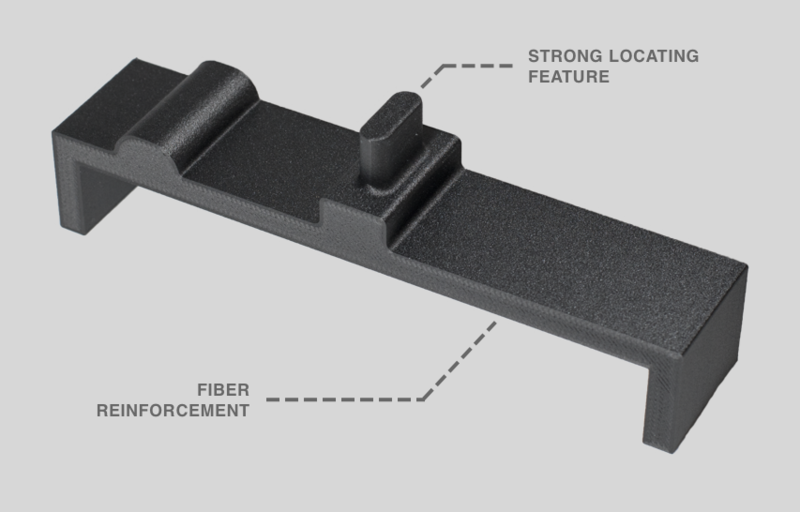
In order to keep up with the pace and shrinking margins of modern manufacturing, looking to additive manufacturing solutions to overcome the need for tool room resources as well as produce iterations quicker is the next step. Markforged customers leverage our composite printers and materials to produce numerous forms assembly fixtures and jigs for a fraction of the cost, time, and resources compared to traditional manufacturing.
Examples include:
- Table-top mounting plates
- Press fit applications
- Custom part carriers and poka-yoke tools
- Welding and soldering fixtures
- SMT masks and assembly
- Fastener-driving assemblies
- G-NG gauges
For a specific application, Eaton Corporation is currently using Markforged printers and composites to create stanchion adapters.
Eaton had tried to traditionally machine its adapters, though no process seemed to yield a part that could withstand the factory’s environment. Its jury-rigged, welded adapter fell apart, while its machined polycarbonate adapter broke with cyclic loading. Once the team started using their Markforged 3D printer, they were able to print a stanchion adapter out of composite materials, including chopped carbon fiber and nylon reinforced with Fiberglass. This part outperformed previous adapters, and cost far less than its machined aluminum counterparts. If you’d like more information about Eaton’s application, check out their application spotlight.
Learn more about different additive manufacturing applications, and how Markforged technology can help.
Request a free sample part today!
All of the blogs and the information contained within those blogs are copyright by Markforged, Inc. and may not be copied, modified, or adopted in any way without our written permission. Our blogs may contain our service marks or trademarks, as well as of those our affiliates. Your use of our blogs does not constitute any right or license for you to use our service marks or trademarks without our prior permission. Markforged Information provided in our blogs should not be considered professional advice. We are under no obligation to update or revise blogs based on new information, subsequent events, or otherwise.
不错过任何一篇文章
订阅以在您的收件箱中获取新的 Markforged 内容