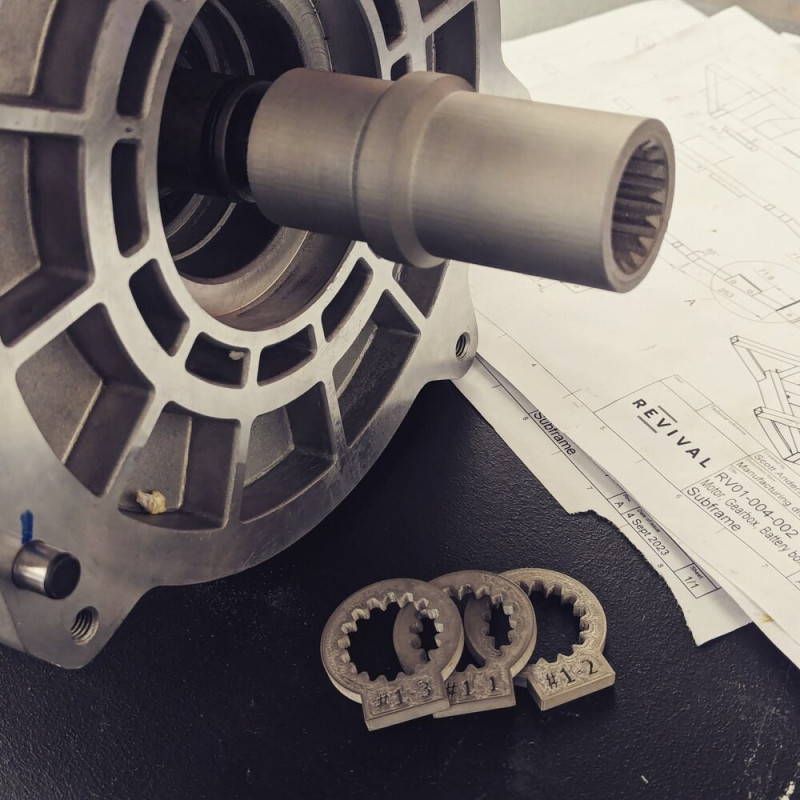
Keilwellenadapter aus Edelstahl
Revival Electric Vehicles, an automotive engineering firm in Melbourne, is developing modular components that facilitate replacing a vehicle’s petrol engine with an all-electric drivetrain and battery modules. They are currently converting a 1972 BMW 2002, which will be their proof of concept and will enable them to commence marketing conversion kits before the end of 2024.
Manufacturing problems arose when dealing with the complexity and tight tolerances required in the spline shaft adapter to link the new motor and gearbox, so Revival called on specialised engineering design company, Bremar, for advice and help.
– Scott Anderson, Managing Director, Revival Electric Vehicles“The time actually spent on the process was probably as little as a week, and the cost was less than a half of what we’d have paid going the conventional route.”
Revival’s managing director, Scott Anderson, said he had previously worked with Bremar during the initial design process, using them to scan the vehicle to help with 3D CAD work, so he was aware of their investment in a suite of industrial 3D printers – a Mark Two™, X7™, FX20™ and Metal X™ supplied by industry leader, Markforged.
“We’re no strangers to 3D printing ourselves. We’ve been using the technology in a small way for nearly 15 years, and more recently used our own Markforged Mark Two™ to print parts of our drive/ neutral/reverse selector, so we had full confidence in Bremar’s ability to produce what we were looking for,” he said.
“I completed the initial design for the adapter and we printed it a few times in PLA to get a feel for the finished item. After discussions with Bremar they printed test parts to ensure the tolerancing was going to be right before producing the finished component. Thin tolerance tests for both ends of the adapter ensured that the final unit worked first time,” he said.
Revival had initially considered using conventional methods – broach milling or electrical discharge machining – to produce the adapter, but were discouraged by the potentially long lead times and the quoted cost of $1,500 for a one-off unit.
“Working with Bremar we were able to go from initial design to final unit in just a few weeks, much of which was taken up with finding the time to drop the motor and gearbox off for tolerance fit testing, so the time actually spent on the process itself was probably as little as a week, and the cost was less than a half of what we’d have paid going the conventional route,” he said.
“We’re confident the finished adapter, printed in 17-4 PH Stainless Steel, will outlast both the motor and the gearbox, and we’re happy to use other 3D printed parts in our builds as we feel they are a great solution for rapid prototyping and testing and are particularly well suited for small scale production,” said Scott.
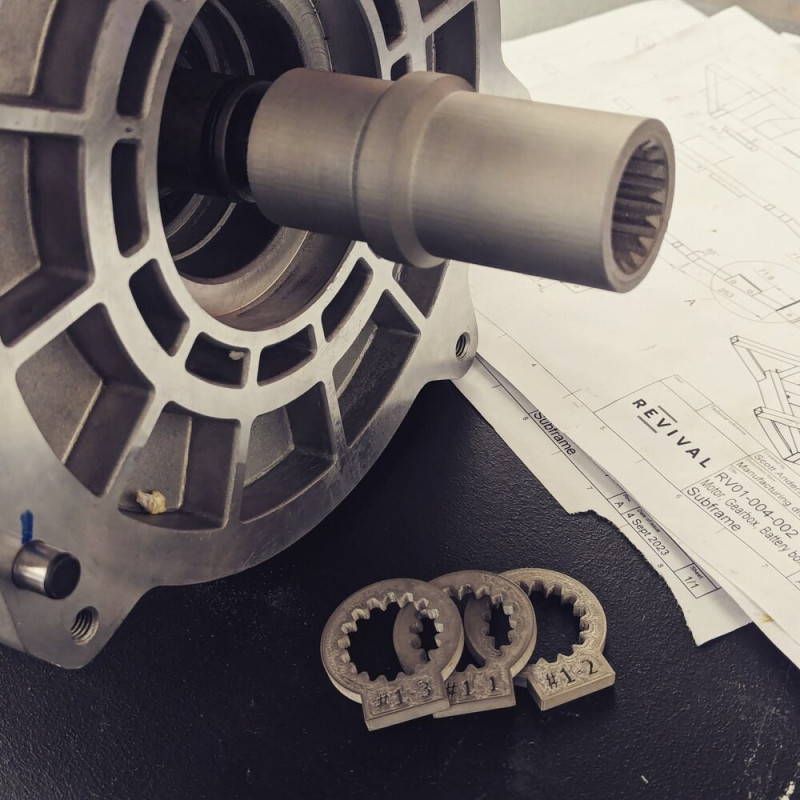
All of the blogs and the information contained within those blogs are copyright by Markforged, Inc. and may not be copied, modified, or adopted in any way without our written permission. Our blogs may contain our service marks or trademarks, as well as of those our affiliates. Your use of our blogs does not constitute any right or license for you to use our service marks or trademarks without our prior permission. Markforged Information provided in our blogs should not be considered professional advice. We are under no obligation to update or revise blogs based on new information, subsequent events, or otherwise.
Never miss an article
Subscribe to get new Markforged content in your inbox