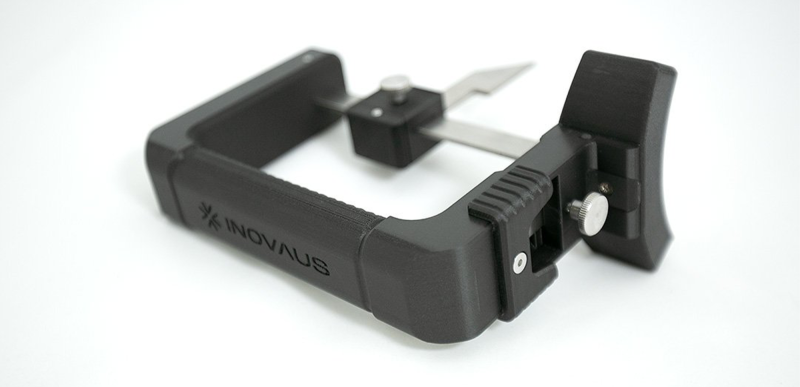
CADDS Group - Messlehre für Zugvorrichtungen
Die CADDS-Gruppe mit Sitz in Westaustralien beschäftigt mehr als 180 Mitarbeiter in ihren sechs Abteilungen Vermessung, Technisches Design, Produktdesign, Gebäudeplanung, Nachhaltiges Umweltdesign und Fertigung. Jede Abteilung deckt ein breites Spektrum an Dienstleistungen für die größten Unternehmen des Bundesstaates ab. Zu den Blue Chip-Kunden aus dem Bergbausektor gehören namhafte Unternehmen wie Rio Tinto, BHP, Alcoa und die Forschungseinrichtung der Australischen Regierung CSIRO[ZH1].
2023 hat die CADDS Group ihre Fähigkeiten durch eine Investition in drei hochmoderne Markforged-Drucker (FX20™, Mark Two™ und Metal X™ ) strategisch erweitert. Mit diesen hochmodernen Geräten ist die Gruppe in der Lage, Teile und Werkzeuge mit hoher Festigkeit und nvergleichlicher Präzision zu fertigen, so Geschäftsführer Darren Clark. Durch die Verwendung neuester Materialien wie Endloscarbonfaser, Edelstahl, Kupfer und Werkzeugstahl katapultiert die Technologie das Unternehmen an die Spitze der Innovation.
Norbert Babooram, Product Design Manager von Inovaus, der Produktdesign-Abteilung der CADDS-Gruppe, sagte, dass sein Team durch den Zugang zu eigenen Druckanlagen im Unternehmen in der Lage ist, schnellere und effizientere Lösungen für die Herausforderungen der Kunden zu entwickeln.
„Als wir unsere Drucker erwarben, kontaktierte uns einer unserer wichtigsten Kunden aus dem Bergbau, um an der Entwicklung eines neuen Werkzeugs zur Messung des Verschleißes an Zugvorrichtungen in Eisenbahnwaggons mitzuwirken“, so Babooram.
Bisher wurde die Messung mithilfe eines Maßbandes und eines Lineals durchgeführt und erforderte den Ausbau der Zugvorrichtung aus der Waggonkupplung, was bei geringer Genauigkeit einen zeitaufwändigen und letztlich kostspieligen Prozess darstellte. Babooram wies darauf hin, dass die geprüften Teile oft innerhalb der Verschleißgrenzen lagen und sie deshalb aufgrund ungenauer Messwerte oft unnötig entfernt wurden.
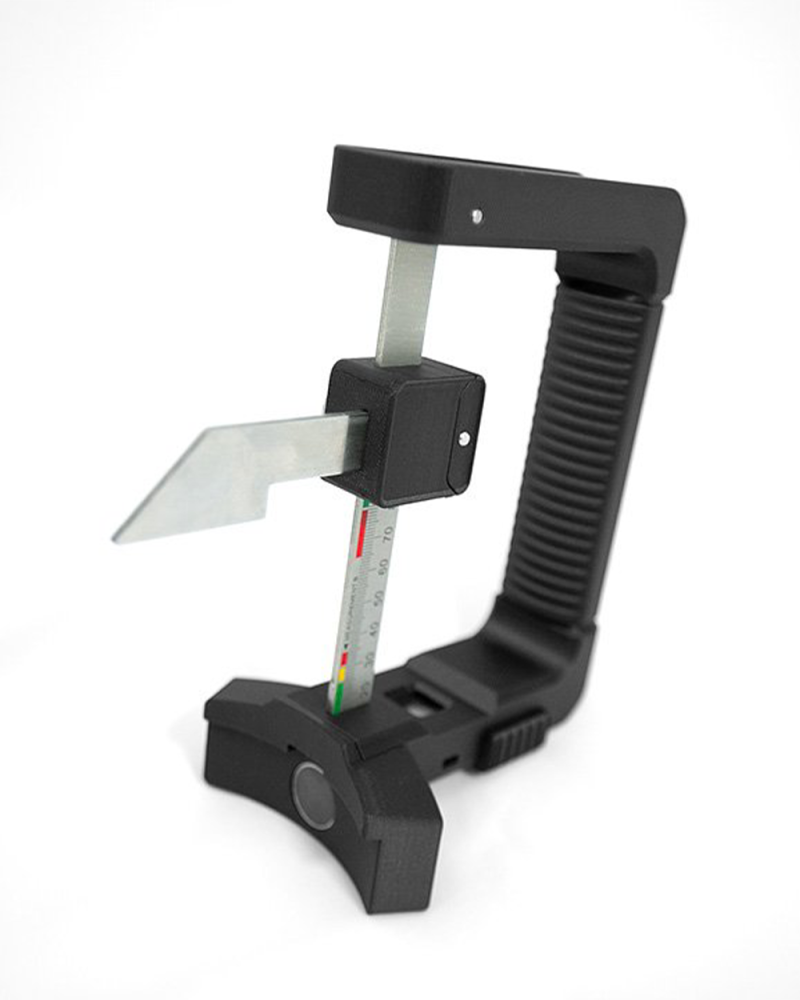
„Der Kunde hatte einen groben Entwurf für ein neues Messgerät erstellt, für das drei unterschiedliche Werkzeuge für verschiedene Teile des Messverfahrens erforderlich waren. Innerhalb einer Woche konnten wir ein einziges Werkzeug entwerfen, welches das gesamte Messverfahren abdecken konnte“, so Babooram.
Über Nacht wurde ein Prototyp auf dem Mark Two gedruckt, bei Inovaus an einer Zugvorrichtung getestet und umgehend an den Kunden zur Prüfung versandt. Das Feedback zum Werkzeug, das vor Ort mehrfach eingesetzt wurde, war überwältigend.
„Wir haben eine zweite Version entworfen und gedruckt, die der Kunde genehmigte und an seinem Standort einsetzte. Dann konnten wir in wenigen Tagen weitere Bauteile entwerfen und ein Werkzeug drucken, mit dem die Zugvorrichtung gemessen werden kann, während sie noch in der Waggonkupplung sitzt“, ergänzte Babooram.
Jede von Inovaus entwickelte Version ist modular aufgebaut, wodurch Änderungen an einzelnen Teilen ohne eine Überarbeitung des gesamten Werkzeugs möglich sind. Bestimmte Bereiche können für unterschiedliche Zugvorrichtungen individuell gestaltet werden.
Baboorams Team berechnete die Kosten und den zeitlichen Aufwand für die Entwicklung und Produktion im Spritzgussverfahren und schätzte, dass der gesamte Prozess einschließlich Entwicklung und Formenbau mindestens 500 Stunden in Anspruch nehmen würde. Die in nur einer Woche in der Additiven Fertigung entworfene Version kann über Nacht gedruckt werden und kostet nur 1,5 % der Gesamtkosten des Spritzgussverfahrens.
„Das Messgerät hat ein immenses internationales Potenzial. Die Entwicklung und Herstellung dieser ersten Modelle dient als Machbarkeitsnachweis und öffnet uns eine Tür im Markt, um auf das Produkt aufmerksam zu machen. Ohne Additive Fertigung wäre dies nicht möglich gewesen“, so Babooram.
Die industrietauglichen 3D-Drucker von Markforged bieten der Bergbauindustrie durch das einzigartige Digital Forge-Ökosystem des Unternehmens wichtige Vorteile, die den Betrieb, die Leitung und die Überwachung von Minenstandorten aus der Ferne ermöglichen. Diese Technologie wird es der CADDS-Gruppe ermöglichen, hochleistungsfähige Teile und Komponenten vor Ort zu produzieren, was die Vorlaufzeiten verkürzt, Stillstandszeiten minimiert und die betriebliche Effizienz insgesamt verbessert.
„Die AM-Version kann über Nacht zu 1,5 % der Gesamtkosten des Spritzgussverfahrens gedruckt werden.“– Norbert Babooram Product Design Manager, Inovaus
All of the blogs and the information contained within those blogs are copyright by Markforged, Inc. and may not be copied, modified, or adopted in any way without our written permission. Our blogs may contain our service marks or trademarks, as well as of those our affiliates. Your use of our blogs does not constitute any right or license for you to use our service marks or trademarks without our prior permission. Markforged Information provided in our blogs should not be considered professional advice. We are under no obligation to update or revise blogs based on new information, subsequent events, or otherwise.
Never miss an article
Subscribe to get new Markforged content in your inbox