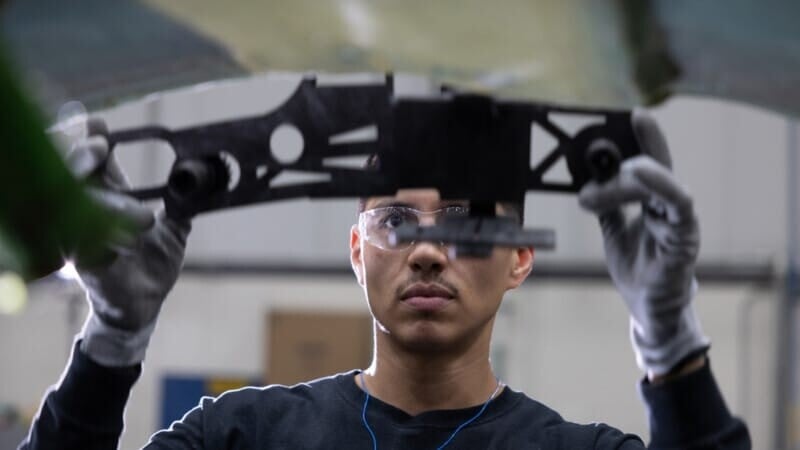
Vestas
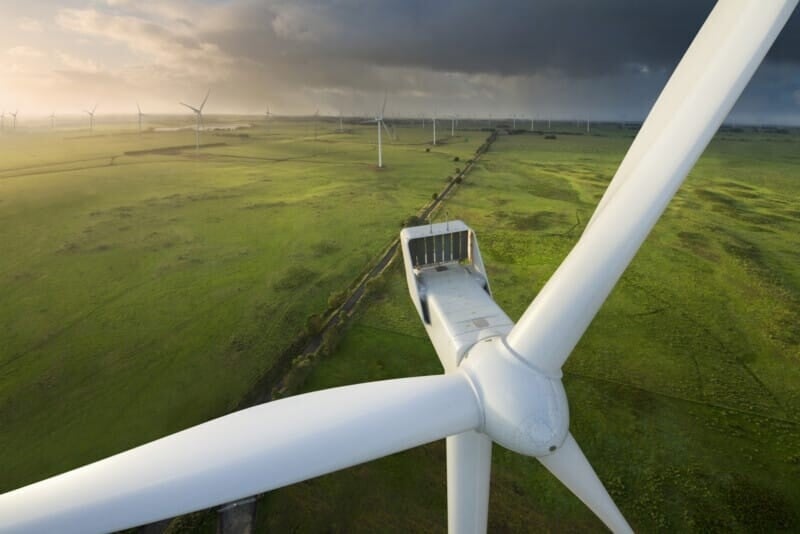
Vestas es una empresa líder mundial en energía eólica. Con más de 151 gigavatios (GW) de turbinas eólicas en 86 países, Vestas genera más energía eólica que sus competidores.
Vestas ha sido calificada como la empresa más sostenible del mundo en 2022, según la lista Global 100 de Corporate Knights.
La estrategia de sostenibilidad de Vestas incluye la producción de aerogeneradores con cero residuos para 2040.
La fabricación aditiva está ayudando a Vestas en su objetivo de alcanzar el cero neto de las emisiones de CO2 en 2030.
El cliente
Entre las tecnologías de energía alternativa, las turbinas eólicas son seguramente las más reconocibles. Con alturas de entre 137 y 259 m y un diámetro de rotor de entre 109 y 236 m, dominan el entorno y suelen ser visibles a kilómetros de distancia. Si alguna vez ha visto un aerogenerador, lo más probable es que haya sido fabricado por Vestas.
Vestas inició su andadura en Dinamarca tras la Segunda Guerra Mundial como una pequeña empresa familiar de fabricación. Durante muchos años, la empresa construyó y suministró sistemas hidráulicos para camiones ligeros. Durante la década de 1970, comenzó a desarrollar soluciones energéticas alternativas y en 1979 construyó su primera turbina eólica comercial. Centrada exclusivamente en la producción de aerogeneradores desde 1989, la empresa diseña, fabrica, instala y repara turbinas eólicas en todo el mundo. En la actualidad, Vestas es el mayor fabricante mundial de palas y aerogeneradores terrestres y marinos. La empresa, con sede en Dinamarca, cuenta con varias sucursales regionales y más de 15 fábricas en todo el mundo.
El desafío
Los aerogeneradores son máquinas enormes y caras que deben funcionar de forma fiable prácticamente sin interrupción para ser lo más eficaces posible. Eso significa que no hay margen de error a la hora de fabricarlos e instalarlos. Por ello, Vestas debe utilizar numerosos medidores de inspección en sus plantas de producción y en los emplazamientos de instalación. Tradicionalmente, estas herramientas esenciales se encargaban a diversos proveedores de todo el mundo, que las fabricaban conforme a unas instrucciones específicas. Las piezas acabadas se enviaban a los distintos centros de Vestas, se inspeccionaban para comprobar su conformidad y, una vez aprobadas, ya se podían utilizar. Lamentablemente, algunas de las piezas finales suministradas por los fabricantes locales no cumplían todas las especificaciones y no pasaban la inspección final, con el consiguiente retraso en las entregas y en la instalación del producto.
Incluso cuando las piezas superaban el proceso de inspección específico, la mayoría se fabricaban con materias primas y métodos de mecanizado tradicionales en un proceso tan lento como costoso. Un ejemplo lo tenemos en las denominadas «Top Center Marking Tools» o herramientas de marcado TC. Estas herramientas esenciales —que Vestas utiliza para marcar el extremo de la raíz de las palas de las turbinas para alinear el pitch— suelen tardar unas cinco semanas en producirse. Por si eso fuera poco, debido a las limitaciones de los diseños mecanizados, el equipo de Vestas tenía que pedir varias versiones de esas herramientas para los distintos tipos de palas. Otro ejemplo son los receptores de rayos, diseñados para reducir los daños que provocan los rayos. Estos receptores, que se construyen en aluminio con el método de fabricación sustractiva, tardan como mínimo 12 semanas en producirse.
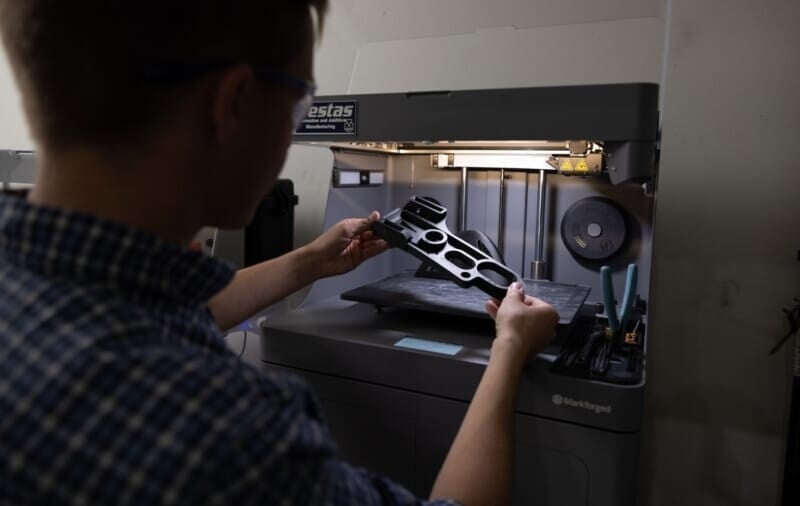
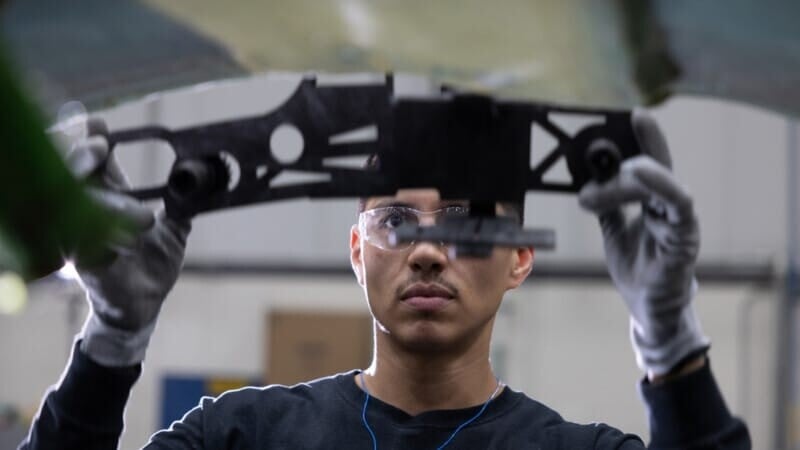
«Vestas está democratizando la fabricación al ponerla en manos de nuestros usuarios finales y mantener un modelo de control de ingeniería centralizado».– Jeremy Haight, Ingeniero jefe de fabricación aditiva y conceptos avanzados, Vestas
La solución
El equipo de Vestas comenzó a estudiar fórmulas alternativas para mejorar su proceso de fabricación general. Mediante la plataforma de fabricación aditiva The Digital Forge de Markforged, basada en la nube y con tecnología de IA, la empresa lanzó con éxito su programa de fabricación digital directa (DDM) en 2021. Este programa libera los procesos de fabricación de la dependencia de proveedores externos y proporciona una base de conocimientos que favorecen la colaboración.
Actualmente, incluye más de 2000 piezas de Vestas almacenadas en un repositorio digital basado en la nube de Markforged Eiger™. De este modo, los empleados de cualquier centro de Vestas —con poca o ninguna experiencia en fabricación aditiva— pueden buscar e imprimir rápidamente piezas de composites reforzadas con fibra en su impresora X7™ y piezas de composites en sus impresoras 3D Onyx One™. Según Jeremy Haight, ingeniero jefe de fabricación aditiva y conceptos avanzados de Vestas, «nuestro sistema es integral. Proporcionamos el artículo físico casi en tiempo real a distintos emplazamientos. Es lo más parecido al teletransporte». Gracias al repositorio, el equipo de Vestas sabe que va a obtener piezas siempre uniformes y de alta calidad en cualquier parte del mundo, sin necesidad de recurrir a especialistas en sus instalaciones globales. Esto no solo ha reducido drásticamente los costes de envío y transporte, sino también los plazos de fabricación.
Para ver algunos ejemplos de cómo funciona la DDM, fijémonos en las herramientas de marcado TC y los receptores de rayos ya mencionados. La herramienta de marcado TC, que antes tardaba semanas en producirse y costaba miles de dólares, ahora se fabrica en pocos días. Y al imprimirse en Onyx, un nylon reforzado con microfibras de carbono tan ligero como duradero, ahora las piezas pesan un 85 % menos que cuando se fabricaban en metal. En cuanto a los receptores de rayos, los centros de fabricación de palas podrán producirlos en cobre impreso en 3D cada vez que lo necesiten. Vestas calcula que, una vez implementado el sistema, cada uno de estos receptores tardará unos dos días en fabricarse. Y lo que es más importante, el equipo de Vestas ya no tiene que preocuparse de que estas u otras piezas no pasen las pruebas de conformidad, ya que se imprimen a demanda en la propia empresa con unas especificaciones digitales exactas. Asimismo, la precisión de las herramientas se verifica durante el proceso con la tecnología de inspección, análisis y elaboración de informes que ofrece la plataforma Blacksmith™ de Markforged.
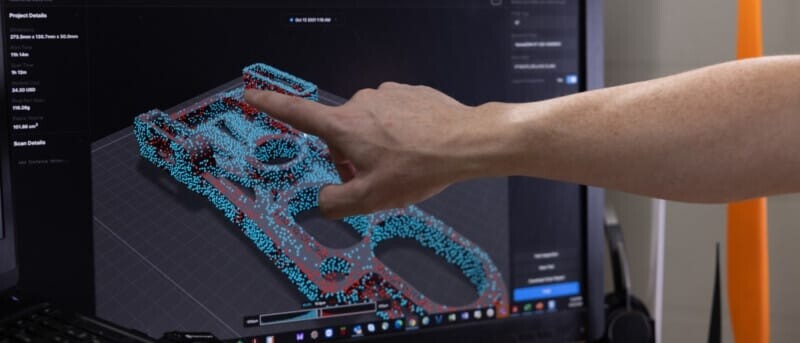
«Elegimos a Markforged porque eran los más capacitados para ofrecernos la solución integral que necesitábamos para lograr nuestra visión de la fabricación digital directa».– Jeremy Haight, Ingeniero jefe de fabricación aditiva y conceptos avanzados, Vestas
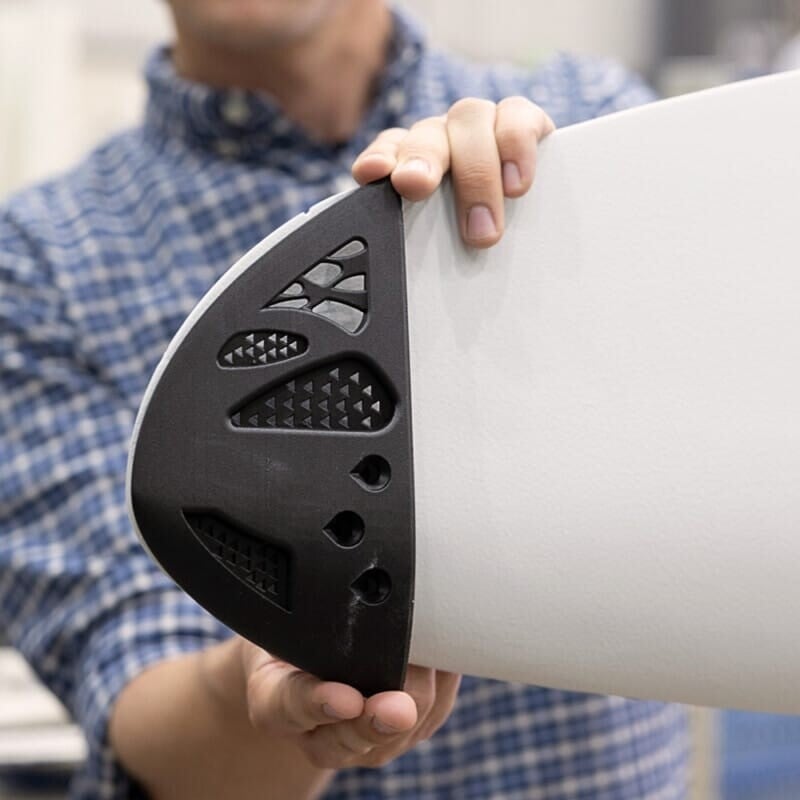
El futuro
Vestas considera que la DDM es fundamental para desarrollar nuevos productos y tener acceso a herramientas y piezas de uso final en toda la empresa. En 2022, se empezará a implantar para los medidores de inspección que se utilizan en las palas con el fin de facilitar su fabricación bajo demanda en los 23 centros de producción. Paralelamente, Vestas también se ha asociado con Würth para crear un ecosistema de fabricación aditiva y gestionar un inventario de piezas de recambio fabricadas con la plataforma The Digital Forge con el fin de facilitar el mantenimiento, la reparación y las operaciones (MRO) de los servicios técnicos sobre el terreno y otros proveedores.
Una vez finalizado el despliegue inicial, Vestas se centrará en aplicar un proceso más profundo y completo en sus instalaciones. La empresa está adoptando medidas para que empleados de cualquier centro de Vestas que cuenten con los permisos necesarios puedan leer un código de pieza o buscarla en sus sistemas de gestión de activos empresariales (EAM) y de planificación de recursos empresariales (ERP) y enviarla automáticamente a la impresora 3D local pertinente. Este control centralizado de los usuarios, las impresoras y la inspección de las piezas mediante Blacksmith y Eiger Fleet™ garantizará la producción de piezas de uso final y herramientas de calidad y alto rendimiento capaces de realizar las tareas para las que han sido diseñadas. Cuanto más favorezca Vestas la producción interna gracias a la fabricación aditiva, más rápidamente llegarán sus productos al mercado y más tiempo y dinero se ahorrará en el proceso.
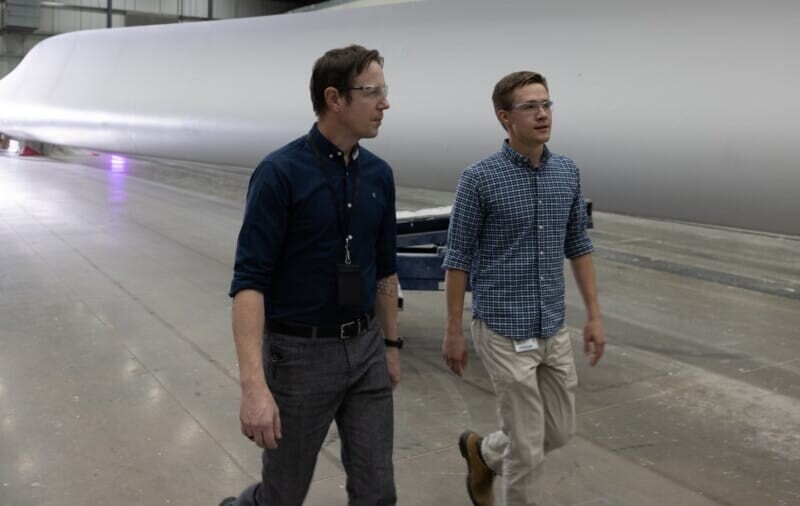
Markforged Partner
Würth
All of the blogs and the information contained within those blogs are copyright by Markforged, Inc. and may not be copied, modified, or adopted in any way without our written permission. Our blogs may contain our service marks or trademarks, as well as of those our affiliates. Your use of our blogs does not constitute any right or license for you to use our service marks or trademarks without our prior permission. Markforged Information provided in our blogs should not be considered professional advice. We are under no obligation to update or revise blogs based on new information, subsequent events, or otherwise.
Never miss an article
Subscribe to get new Markforged content in your inbox