Markforged Resources
Application Spotlights
Application Spotlights
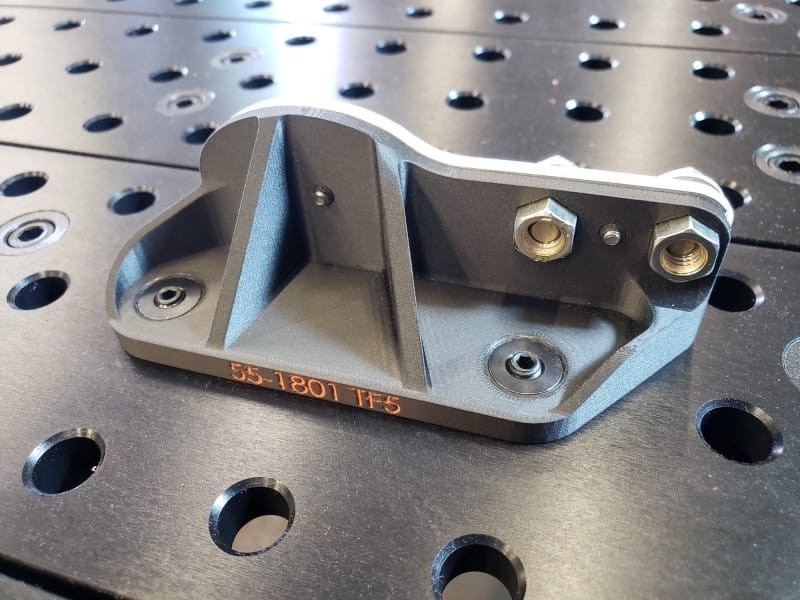
SDHQ: Welding Fixture
SDHQ Shortened their R&D process greatly by replacing costly machined welding fixtures with Markforged 3D printed ones.
Application Spotlights
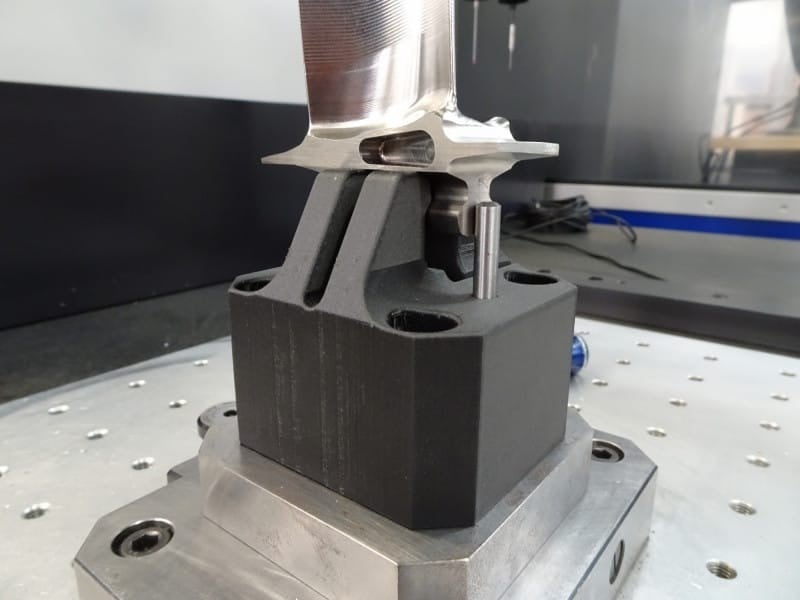
JJ Churchill: CMM Inspection Fixture
JJC can design and test fixtures within the same week, with lower material waste and exceptional quality and precision.
Application Spotlights

Arc34: High Strength Camera Mount
Arc34 Uses continuous Fiberglass and Chopped Carbon Fiber to manufacturing end use GoPro mounts. Their low volume and high strength requirements make Markforged printers a perfect option.
Application Spotlights
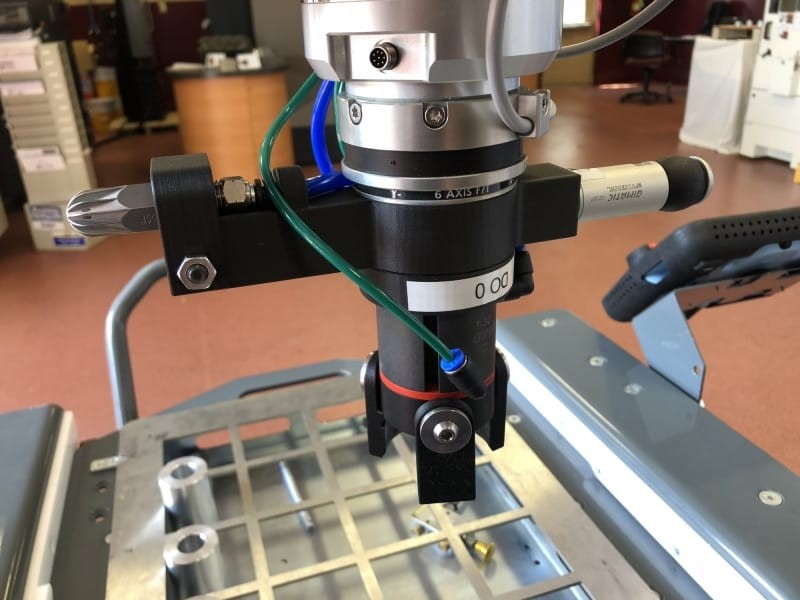
ProCobots: Robotic End Effectors
ProCobots streamlines its customers’ manufacturing workflows by minimizing overhead and maximizing effectiveness.
Application Spotlights
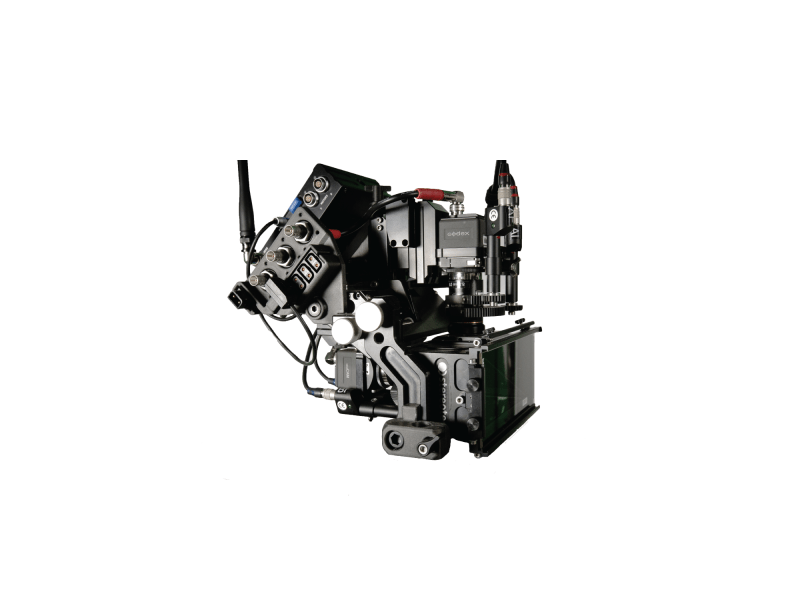
Rent the Sky Films: Camera Cable Harness
Rent the Sky Films uses Markforged to print cable mounting for a handheld 3D camera. The part must provide a single-point adapter for eight critical ports on the camera.
Application Spotlights
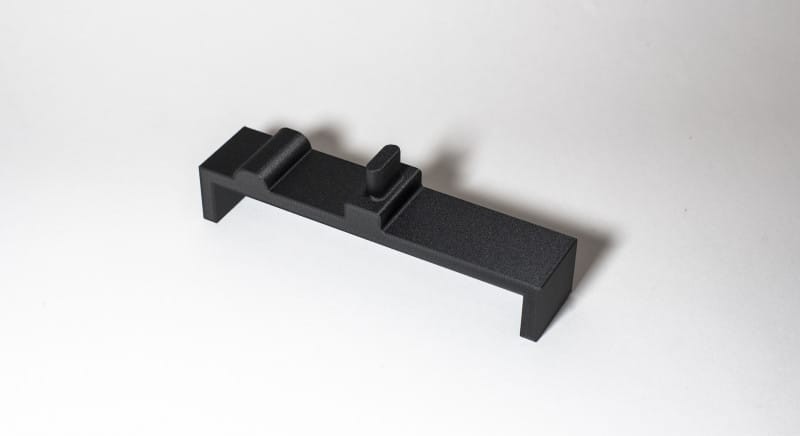
Eaton: Stanchion Adapter
Eaton fabricates assembly line stanchion adapters that constrain plastic clips as operators press hydraulic pipes into them.
Application Spotlights
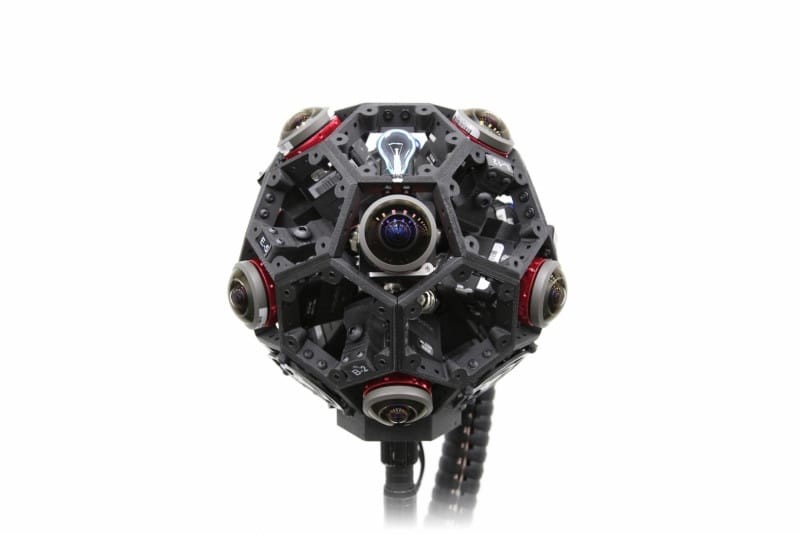
Radiant Images: Camera Frame
Radiant Images prints the entire frame of the AXA 360 camera rig with Markforged. The frame consists of high strength printed polygonal brackets bolted together at an angle.
Application Spotlights
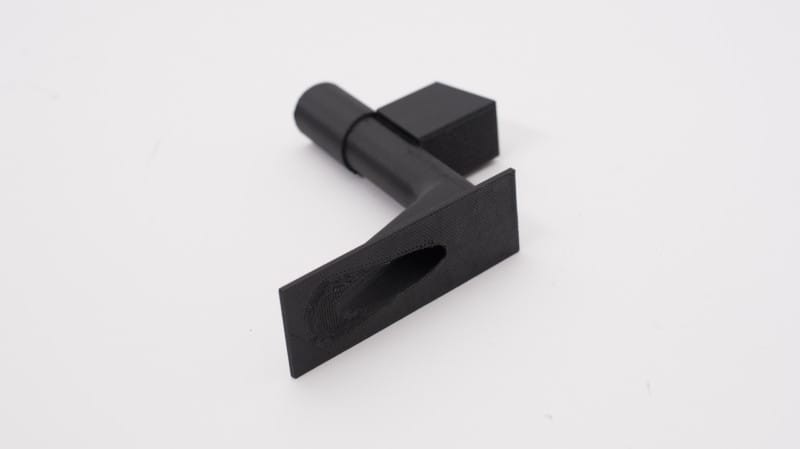
MARTAC: Seawater Intake
MARTAC prints water intakes for autonomous aquatic vehicles that pull seawater from outside the vehicle to cool the vehicle's motors.
Application Spotlights
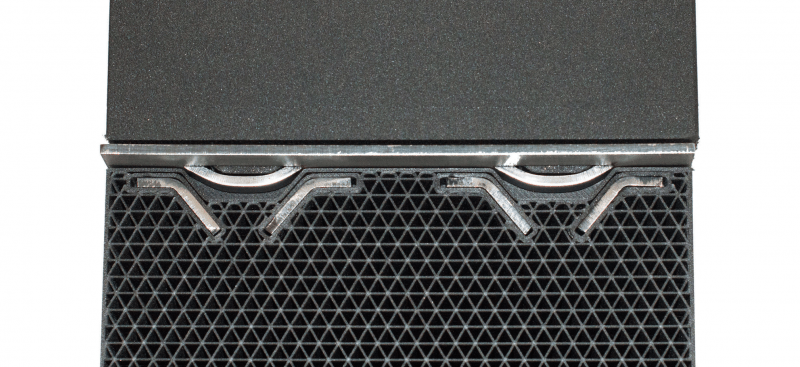
Centerline Engineering Solutions: Press Brake Punch
Centerline Engineered Solutions prints forming dies for sheet metal fabrication. The printed die and punch mount on a press brake, which forms 14 gauge steel.
Application Spotlights
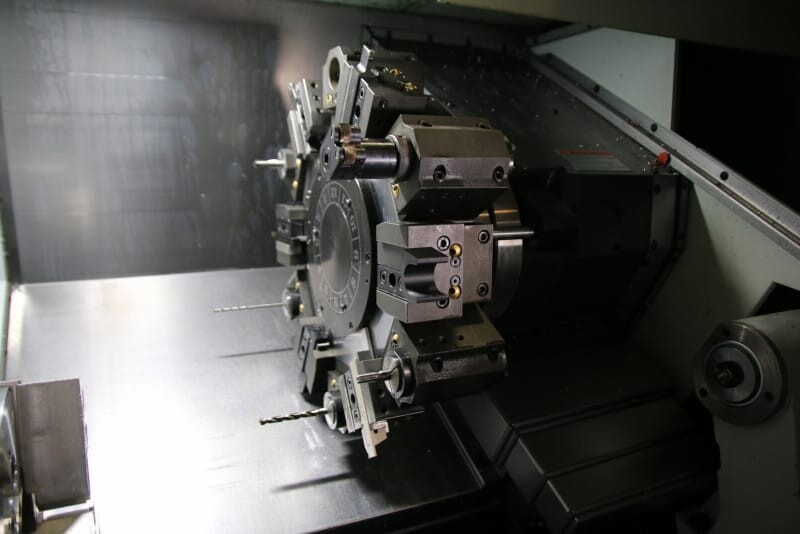
bmi CAD: CNC Lathe Bar Puller
bmi CAD uses Markforged to print feed stock automation tools for a CNC lathe. Each puller is turret mounted and uses friction to move heavy metal feedstock.