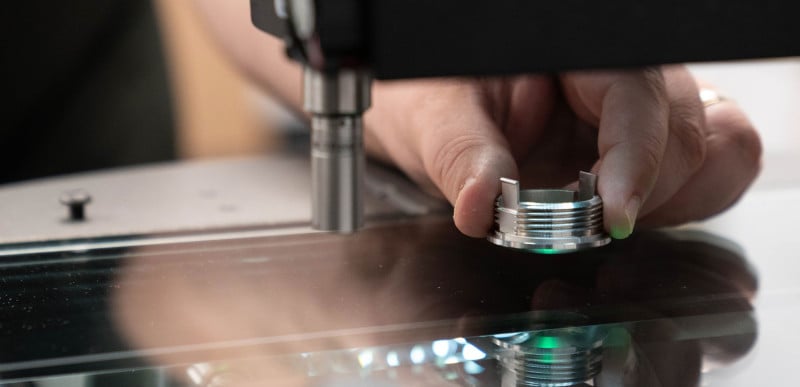
PTI Tech
Acelere el prototipado de MIM con la inyección de aglutinante metálico
El desafío
PTI Tech es un fabricante por contrato global de componentes de precisión moldeados por inyección especializado en polímeros de ingeniería y la tecnología MIM (Metal Injection Molding). En este último proceso, el metal en polvo se mezcla con un aglutinante y luego se inyecta en la cavidad de un molde a alta presión. Las piezas en «verde» deben someterse a un proceso de desaglomerado y sinterización, con el que se obtienen piezas metálicas de alta calidad y densidad.
PTI Tech está especializado en la fabricación de piezas complejas de alta precisión para sectores esenciales, como la industria aeroespacial, defensa, dispositivos médicos y aplicaciones industriales de gama alta. PTI somete los diseños de las piezas de sus clientes a un proceso de fabricabilidad (DFM) con el fin de garantizar que puedan fabricarse de forma rentable mediante moldeo por inyección de plástico o metal.
Un importante fabricante de ascensores utilizaba tapas y cuerpos de botones de acero inoxidable con un conjunto de plástico sobremoldeado. La limpieza con desinfectantes fuertes estaba agrietando y deteriorando las roscas de plástico. El fabricante tenía la necesidad urgente de rediseñar el cuerpo del botón y la tapa como un conjunto totalmente metálico más duradero utilizando acero inoxidable 316L.
Necesitaba sacar estas piezas al mercado con rapidez para poder adaptarlas sobre el terreno a los ascensores existentes. El diseño del cuerpo del botón incluía un par de lengüetas de retención flexibles que debían ser lo bastante finas como para poder flexionarse con la mano pero conservar su forma sin agrietarse.
PTI Tech necesitaba una tecnología de fabricación capaz de producir una serie de piezas representativas de la producción que su cliente pudiera utilizar para probar y validar los diseños. Estas piezas debían tener unas características físicas y de procesamiento similares a las de las piezas producidas por MIM para que PTI Tech pudiera finalizar su diseño antes de construir los moldes de producción.
«La contracción y la densidad final que conseguimos con las piezas inyectadas con aglutinante son muy similares a las de las piezas metálicas moldeadas por inyección»— Gaetano Mariella, Director de Tecnología

La solución
La inyección de aglutinante metálico y el moldeo por inyección de metal tienen varias similitudes: Ambos son procesos de polvo metálico sinterizado que producen piezas con propiedades mecánicas similares, según un informe elaborado por PTI Tech. También presentan un comportamiento similar de contracción durante la sinterización.
PTI Tech seleccionó el sistema de inyección de aglutinante de Markforged para producir rápidamente una serie de prototipos de conjuntos de botones de ascensor para que el cliente los probara. Según Neal Goldenberg, presidente de PTI Tech, produjo piezas que tenían un porcentaje de contracción durante la sinterización, una densidad y un acabado superficial similares a los de las piezas producidas mediante moldeo por inyección de metal. La pieza cumplía los requisitos, destacando una paridad significativa con la pieza final de MIM. Las lengüetas flexibles y varias morfologías de paredes delgadas cumplían los requisitos de durabilidad de PTI, garantizando que no se romperían durante las instalaciones sobre el terreno.
Sin la inyección de aglutinante metálico, PTI Tech habría tenido que construir una serie de moldes de preproducción para probar diversos grosores de lengüeta y otras variables de diseño de las piezas. Según Goldenberg, el proceso habría durado hasta 16 semanas, obligando a fabricar un nuevo molde para cada iteración. Gracias a la inyección de aglutinante metálico, PTI Tech pudo llevar a cabo un minucioso proceso de DFM y, aun así, entregar al cliente varias tandas de 275-300 piezas de preproducción para que las probara, sin necesidad de moldes, en solo cuatro semanas.
El equipo de ingenieros del cliente pudo realizar pruebas funcionales y destructivas. También pudieron analizar el rendimiento estructural de los prototipos y hacer retoques en su estética y dimensiones, sin invertir en moldes fijos. Una vez finalizado el diseño, el cliente pudo encargar los moldes de MIM con mayor confianza.
Al eliminar estos pasos, el equipo de PTI Tech calcula que el uso de la inyección de aglutinante para producir prototipos funcionales supuso un ahorro de costes de más de seis cifras y varios meses de desarrollo. Este rápido proceso de desarrollo satisfizo la necesidad del fabricante de suministrar rápidamente estas piezas mejoradas. También reforzó la reputación de PTI Tech al poder entregar al cliente piezas de alta calidad en plazos cortos, y aumentó la confianza del cliente en la capacidad de PTI para suministrar piezas de producción de forma urgente.
El futuro
Muchos de los encargos de PTI Tech suponen un reto para la fabricación de piezas que requieren una profunda reflexión y una amplia resolución de problemas. La posibilidad de construir rápidamente una serie de prototipos representativos de MIM permite a su equipo probar ideas y realizar iteraciones para llegar a una solución mucho más rápido que mecanizando las piezas o creando moldes de MIM de preproducción para fabricarlas.
Este proceso también da al equipo de PTI Tech una mayor confianza en el diseño del molde antes de cortar el acero para fabricar una herramienta de producción de metal, además de reducir el riesgo.
Dado que la inyección de aglutinante metálico puede proporcionar a los clientes de PTI Tech piezas listas para la preproducción con tanta rapidez, PTI Tech cree que pronto se utilizará en lugar del mecanizado para crear prototipos de piezas para muchos de sus clientes. La inyección de aglutinante también podría utilizarse para series limitadas mediante moldes piloto, de modo que los clientes puedan comenzar el montaje mientras se fabrican los moldes de producción. Además, puede utilizarse para producir piezas de uso final de menor volumen en casos en que el coste de los moldes para el moldeo por inyección de metal puede ser prohibitivo.
Teniendo en cuenta el ahorro de tiempo y costes que supuso el proyecto del botón de ascensor, PTI no duda de que la inyección de aglutinante representa una importante ventaja competitiva para PTI Tech y sus clientes.
«La inyección de aglutinante nos permite reducir el tiempo de desarrollo y probar varias ideas en paralelo, finalizar el diseño de la pieza y pasar directamente a los moldes de producción».— Neal Goldenberg, Presidente

All of the blogs and the information contained within those blogs are copyright by Markforged, Inc. and may not be copied, modified, or adopted in any way without our written permission. Our blogs may contain our service marks or trademarks, as well as of those our affiliates. Your use of our blogs does not constitute any right or license for you to use our service marks or trademarks without our prior permission. Markforged Information provided in our blogs should not be considered professional advice. We are under no obligation to update or revise blogs based on new information, subsequent events, or otherwise.
Never miss an article
Subscribe to get new Markforged content in your inbox