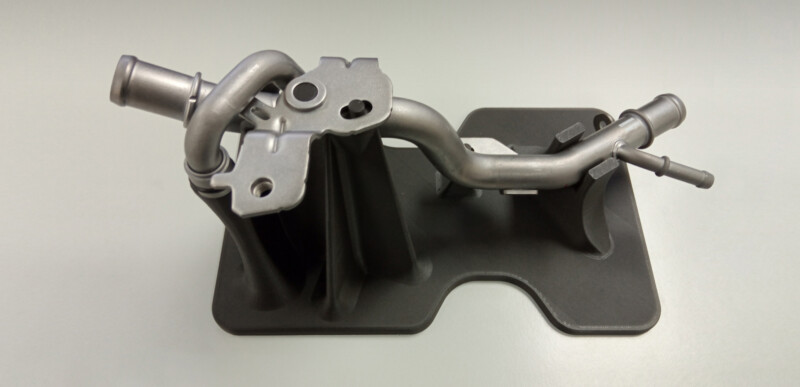
Manufactura Moderna de Metales (MMM)
Le Client
Manufactura Moderna de Metales (MMM) est un fabricant de composants automobiles qui développe des solutions technologiques innovantes axées sur la transition énergétique, en s'appuyant sur la réputation de fiabilité et de sécurité d'une entreprise forte de plusieurs dizaines d'années d'expérience dans le secteur exigeant des transports. MMM partage activement depuis plus de 75 ans sa vision long terme des changements à venir dans le secteur des transports, en consacrant des ressources humaines et financières destinées à répondre aux problématiques de conception. L’entreprise compte aujourd’hui des usines en Roumanie, au Mexique et en Espagne.
Les différentes divisions du groupe MMM proposent des solutions et conçoivent des systèmes qui répondent aux normes de qualité et de sécurité les plus strictes :
Systèmes de fluides : MMM fabrique des tubes en acier, en acier inoxydable et en aluminium pour l’industrie automobile. La division Systèmes de fluides s'est forgée une solide réputation grâce à ses produits développés pour le traitement des fluides dans des environnements exigeants. Elle fournit les principaux constructeurs automobiles depuis plus de 50 ans.
Systèmes énergétiques : MMM est spécialisée dans la conception de solutions efficaces et innovantes - aux applications multiples et transsectorielles - destinées à soutenir la transition énergétique et la décarbonation dans une grande variété de secteurs d’activité. MMM contribue à cette transition et à cette décarbonation par la fabrication et la vente de technologies de capture d'hydrogène et de CO2.
ADDiVAL : Services d'impression additive pour des entreprises tierces ainsi qu'une assistance technique visant à garantir que le produit final est adapté à chaque besoin client.
Principaux clients : Stellantis, Toyota, Suzuki, BMW, Groupe Volkswagen, Renault et Nissan.
En 2021, MMM a diversifié ses services en créant deux nouvelles divisions : la division Énergie, spécialisée dans la production d'hydrogène, et la division Fabrication additive.
The Challenge
C'est dans ce contexte que MMM a décidé d'intégrer la fabrication additive à sa division d'impression 3D :
« En 2019, notre recherche permanente de leviers d'innovation et d'excellence nous a conduits à intégrer la technologie 3D dans nos processus de production.
C’est à cette période que nous avons entamé une recherche de solutions et de systèmes complets qui permettraient d’offrir une plus-value par rapport à nos concurrents », explique Borja Batlle, responsable du développement commercial au sein du département ADDiVAL.
L’objectif principal était de réduire notre temps de réponse de 6 à 2 semaines.
Nous avions besoin de systèmes industriels de haute précision pour simuler les conditions dans lesquelles nos composants automobiles fonctionneraient une fois installés dans le moteur des véhicules. Un des tests auxquels les composants devaient être soumis était le test de vibration. La difficulté consistait à réduire le poids des dispositifs de fixation sans pour autant compromettre leur aptitude à passer ces tests.
Un autre défi consistait à créer des outils de cintrage de tubes métalliques dès la phase de développement afin de réduire les délais et les coûts associés aux nouveaux projets.
Nous devions également concevoir de nouvelles cales et d'autres outils de contrôle pour les besoins de production et de développement.
Principaux besoins :
+ Fabriquer des dispositifs de fixation pour l'entreprise
+ Imprimer des tubes de manipulation de fluides pour les moteurs, les systèmes d'air conditionné et les circuits d'eau
« Ces tubes présentent différents diamètres et coûtent cher. Ainsi, lorsque vous pouvez imprimer le tube et valider les cales, obtenir les bons diamètres et les dispositifs de fixation adéquats afin de simuler l’assemblage et le montage au cours de la production, vous disposez d’un avantage formidable que vous pouvez offrir à vos clients », poursuit M. Batlle.
« Nous sommes parvenus à concevoir des pièces qui sont imprimées en trois semaines et qui permettent de valider l’ensemble du processus ».
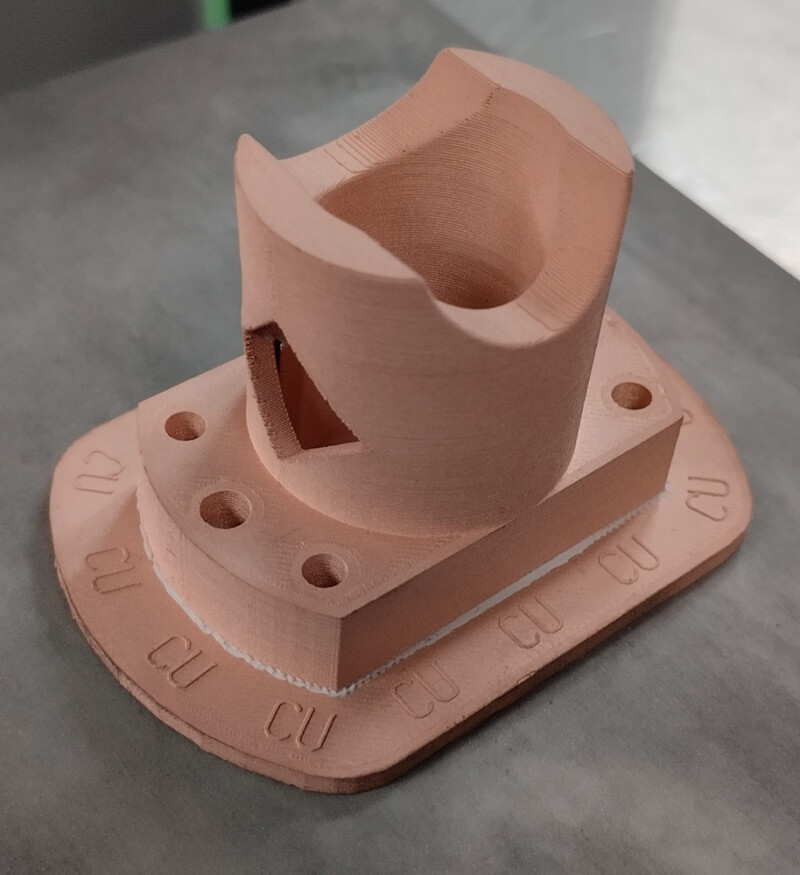
« Autre exemple provenant de notre usine roumaine : un dispositif de contrôle de manchons en caoutchouc. Nous avons conçu un mécanisme à l'intérieur de la structure avec une vis sans fin. Grâce à la fabrication de haute précision, le dispositif a pu être utilisé pour contrôler l’écart maximal de 1,0 mm aux extrémités du tube », ajoute M. Batlle.
« Cet écart, qui détermine le degré de précision nécessaire pour définir la tolérance d’une pièce, a permis de gagner 60 % du temps total de cycle. Ce type de mécanisme ne peut être réalisé avec des méthodes traditionnelles. Nous ne pouvons obtenir ce résultat qu’avec des constructions composites », explique M. Batlle.
La Solution
Pour compléter sa capacité de fabrication de pièces, MMM a fait l’acquisition d’une imprimante 3D Markforged qui peut imprimer des pièces résistantes, renforcées notamment en fibre de verre continue et en composites à base de fibres de carbone.
MMM a constaté que l’imprimante 3D de la série industrielle X7 était extrêmement polyvalente et qu’elle permettait de produire des pièces de haute précision extrêmement résistantes dans des délais très courts. C'est aussi l’un des avantages du renforcement par fibres continues au cours du processus de fabrication. L’entreprise utilisait auparavant l’imprimante 3D pour fabriquer les prototypes de ses composants, mais elle l’utilise désormais pour concevoir et fabriquer des composants finaux, directement au sein de son site de production.
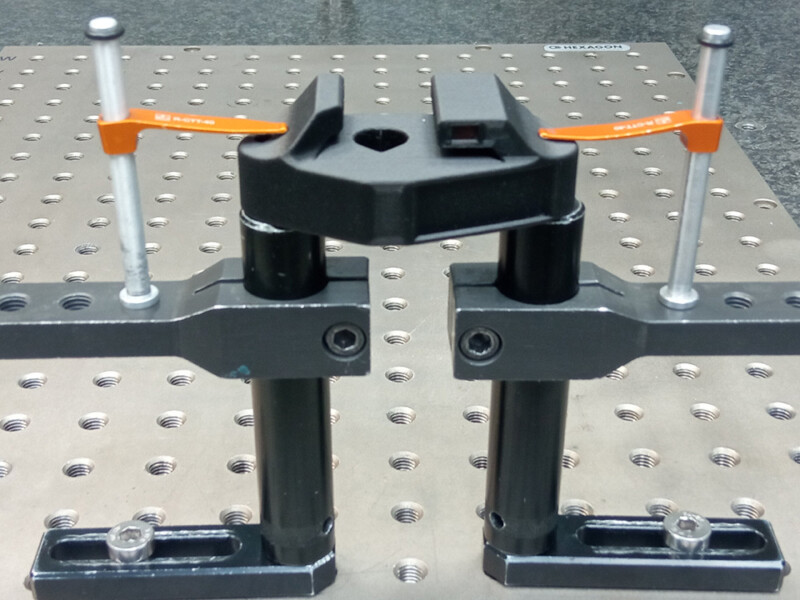
« Nous avons étudié plusieurs solutions d’extrusion de matériaux et de frittage et nous avons réalisé des essais ciblés. Les systèmes Markforged nous ont donné les meilleurs résultats en termes de compromis entre facilité d’utilisation, précision et polyvalence », nous a expliqué M. Batlle.
Le projet a également été déployé grâce à une imprimante 3D de la série Metal de Markforged : la Metal X.
« L’imprimante Metal X est venue renforcer notre processus de création de composants en réduisant le temps de production des pièces. Cela a permis d’accélérer la livraison et la commercialisation de nos produits comparativement à l’usinage CNC. »
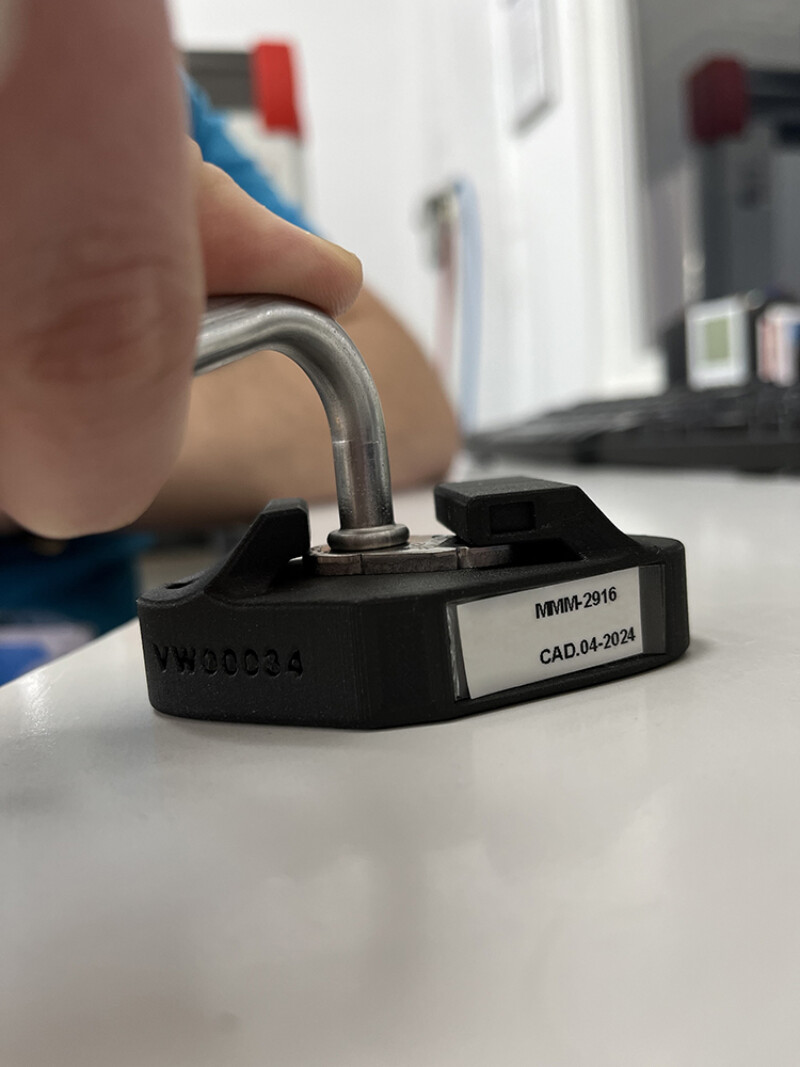
« Chez Manufactura Moderna de Metales, nous utilisons désormais les composants que nous fabriquons avec les imprimantes X7 et Metal X et nous les combinons pour créer des montages hybrides très résistants et légers. Nous combinons par exemple les cales et autres dispositifs de contrôle de jeu avec des pièces fabriquées avec l’imprimante Metal X », explique M. Batlle.
« L’objectif de cette nouvelle division est d’aider nos clients à identifier les maillons de leur chaîne de valeur dans laquelle la fabrication additive pourrait produire un véritable effet de levier et leur apporter une plus forte valeur ajoutée. »
« Pour ce faire, nous nous appuyons sur une équipe d’ingénieurs spécialisés qui accompagnent nos clients dans l’analyse de leurs projets et leur permettent d’obtenir les meilleurs résultats possibles. En conjuguant notre expérience et la technologie de fabrication additive 3D, nous pouvons trouver la meilleure solution qui répondra aux besoins de nos clients via l’impression 3D », souligne M. Batlle.
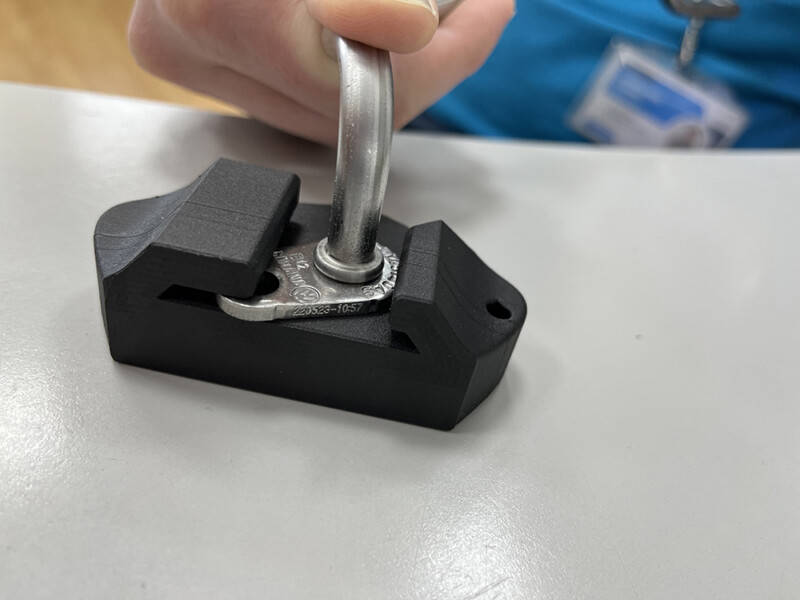
« Nous avons utilisé de l’acier inoxydable 17-4PH et de l’acier à outils H13 avec notre imprimante Metal, même si nous sommes plus particulièrement spécialisés dans les composants en cuivre pour obtenir des pièces de haute conductivité », poursuit M. Batlle.
Certaines des pièces imprimées en cuivre sont utilisées comme électrodes de soudage.
« Près de 20 % des pièces que nous fabriquons sont destinées au contrôle de nos standards internes, alors que les 80 % restants sont essentiellement produits pour des clients dans le secteur de l’emballage. »
M. Batlle ajoute que chez MMM, les pièces composites sont principalement destinées à la maintenance préventive, car il est alors question de pièces d’usure ou de pièces en fin de vie. Un très haut niveau de précision a été atteint, avec des pièces présentant des écarts de 0,05 mm. Ces résultats sont à la fois le fruit de la performance des systèmes d’impression et de stratégies spécifiques de méthodes de conception pour la fabrication additive (DFAM - Design for Additive Manufacturing).
« Notre plus grand défi a été de nous familiariser avec la technologie et de l’utiliser de façon optimale ».
Conclusions
MMM est plus que jamais convaincue que l’impression 3D peut être utilisée pour produire des gabarits, des outils et d’autres pièces uniques, et qu’elle est la réponse optimale aux projets présentant ce type de contraintes.
+ Besoin de pièces très spécialisées
+ Réduction significative des délais de développement et de réalisation de pièces finales
+ Besoin de flexibilité au cours du processus de conception et tout au long du processus de fabrication
+ Réalisation de systèmes de clipsage et de mécanismes en utilisant la méthode DfAM
+ Impression de plus de 50 structures identiques, ce qui démontre la répétabilité de la solution
+ Pièces finales d'une précision maximale
+ Des pièces peuvent être fabriquées afin de tester la qualité des composants
+ Obtention de dispositifs de fixation sans recours à l'usinage
« Au cours des cinq dernières années, nous avons réduit nos délais de livraison de composants de 58 jours en moyenne à seulement 14-21 jours, voire 3 jours dans certains cas. Un véritable succès ! » explique Borja Batlle.
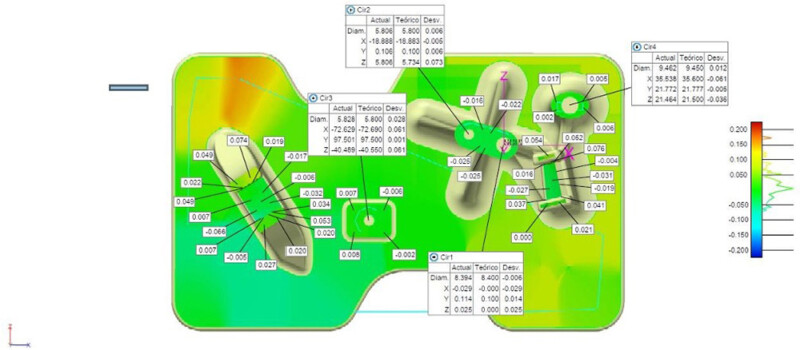
Demain
« Notre dynamisme, notre proactivité et notre expertise sont nos principaux leviers de réussite dans cette nouvelle ère d’innovation et de déploiement de nouvelles solutions ». Groupe MMM.
MMM précise que sa spécialisation dans le cuivre lui a offert de nouveaux débouchés dans le secteur de l’emballage.
« La prochaine étape consistera à étudier le potentiel de production de la FX20, car nous devons augmenter notre productivité et la taille de nos pièces », commente M. Batlle.
« Nous devons développer notre division d’impression 3D et nous prévoyons de créer une nouvelle zone dédiée au sein de notre établissement. En ce sens, la FX20 est une solution tout à fait intéressante. »
« Pour résumer mon expérience, à ce jour, avec les technologies Markforged, je dirais en un mot : PRÉCISION », conclut-il.
En savoir plus sur la fabrication additive avec Markforged
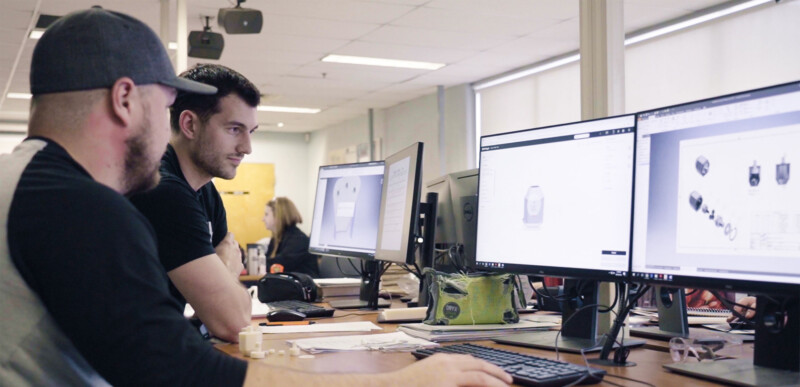
Université de Las Palmas - Grande Canarie
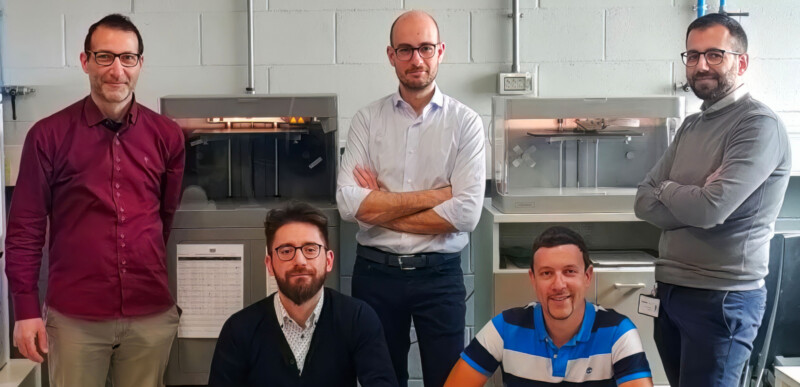
PUNCH Torino
All of the blogs and the information contained within those blogs are copyright by Markforged, Inc. and may not be copied, modified, or adopted in any way without our written permission. Our blogs may contain our service marks or trademarks, as well as of those our affiliates. Your use of our blogs does not constitute any right or license for you to use our service marks or trademarks without our prior permission. Markforged Information provided in our blogs should not be considered professional advice. We are under no obligation to update or revise blogs based on new information, subsequent events, or otherwise.
Never miss an article
Subscribe to get new Markforged content in your inbox